Stellen Sie sich eine Art der Herstellung vor, bei der nichts verschwendet wird, jeder Schritt das Produkt verbessert und Sie alle Ihre Ressourcen sinnvoll nutzen. Das ist die Essenz der schlanken Fertigung. Wenn Sie sich jemals gefragt haben, wie es einigen Unternehmen gelingt, mit weniger mehr zu produzieren, werden Sie gleich die Geheimnisse entdecken. In diesem blog Posten, wir werden erkunden
Die 5 Grundprinzipien der Lean Manufacturing
Wir nehmen Sie mit auf eine Reise durch die Art und Weise, wie sie vielen Unternehmen auf der ganzen Welt geholfen hat.
Inhaltsverzeichnis
Was ist Lean Manufacturing?
Vorteile von Lean Manufacturing
Die 5 Prinzipien der Lean Manufacturing
Abschließende Überlegungen
FAQs zu den Prinzipien der Lean Manufacturing
Was ist Lean Manufacturing?
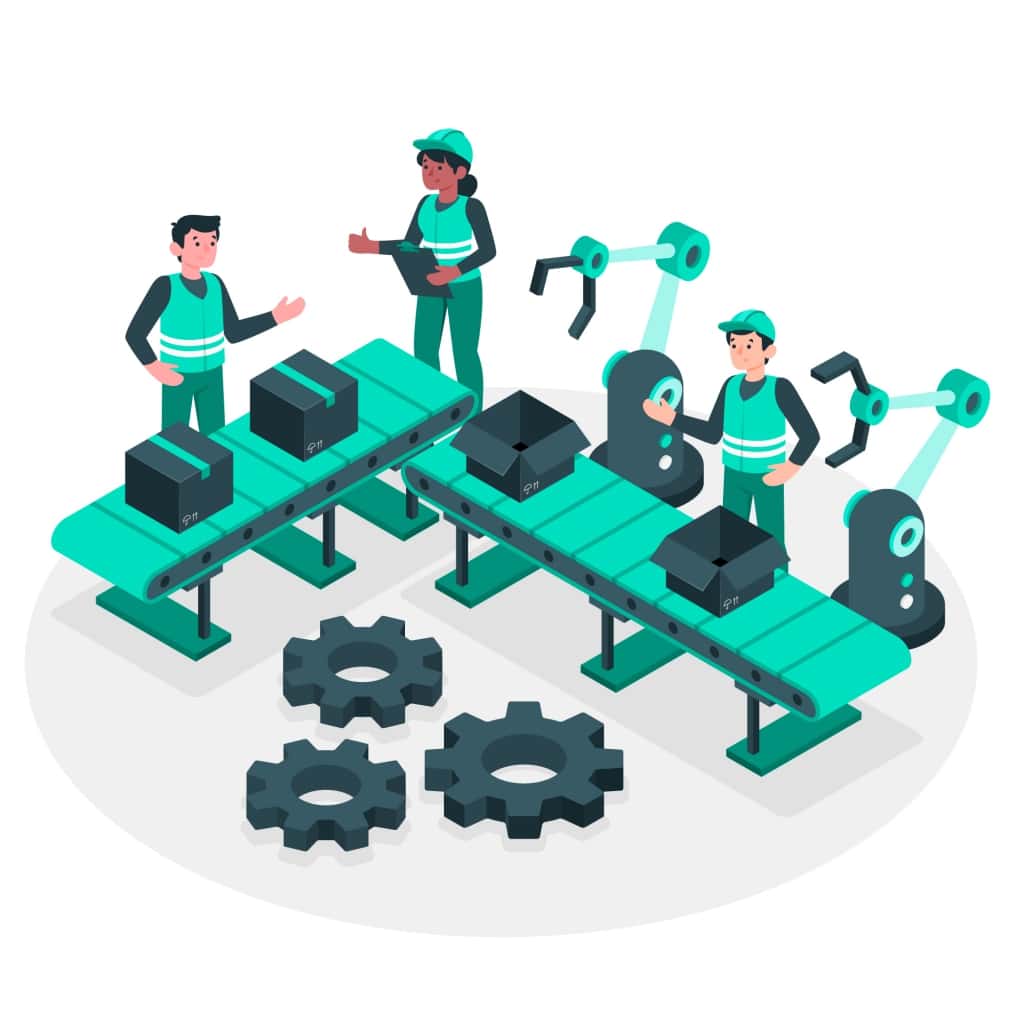

Lean Manufacturing ist ein systematischer Produktionsansatz, der darauf abzielt, Verschwendung zu reduzieren, die Effizienz zu steigern und den Kunden einen Mehrwert zu bieten. Dieser Ansatz stammt aus der
Toyota Produktionssystem (TPS)
und wurde inzwischen weltweit von verschiedenen Branchen und Unternehmen übernommen.
Das Hauptziel von Lean Manufacturing besteht darin, den Produktionsprozess zu vereinfachen, indem unnötige Aktivitäten, Materialien oder Ressourcen identifiziert und entfernt werden, die nicht direkt zum Endprodukt oder zur Dienstleistung beitragen. Dies trägt dazu bei, den Prozess zu rationalisieren und effizienter zu gestalten.
Vorteile von Lean Manufacturing
Lean Manufacturing bietet Unternehmen, die ihre Abläufe verbessern möchten, mehrere Vorteile. Hier sind fünf wesentliche Vorteile:
Kosteneinsparungen
: Lean Manufacturing identifiziert und eliminiert Verschwendung in Prozessen und senkt dadurch die Betriebskosten. Dazu können niedrigere Lagerhaltungskosten, ein geringerer Energieverbrauch und weniger Nacharbeit gehören, was letztendlich den Unternehmensgewinn steigert.
Effizienz erhöhen:
Durch die Rationalisierung von Prozessen, die Beseitigung von Engpässen und die Optimierung von Arbeitsabläufen steigert Lean Manufacturing die betriebliche Effizienz. Das bedeutet, dass Unternehmen mit der gleichen oder weniger Ressourcenmenge mehr produzieren und so den größtmöglichen Nutzen aus ihren Investitionen ziehen können.
Verbesserte Qualität:
Lean Manufacturing konzentriert sich auf die Identifizierung und Behebung der Grundursachen von Fehlern, was zu einer höheren Produktqualität führt. Das bedeutet weniger Fehler, weniger Nacharbeit und eine höhere Kundenzufriedenheit.
Schnellere Lieferung:
Lean-Praktiken führen zu kürzeren Vorlaufzeiten und einer schnelleren Reaktion auf Kundenbedürfnisse. Die Fähigkeit, Produkte pünktlich zu produzieren und zu liefern, kann Unternehmen dabei helfen, sich einen Wettbewerbsvorteil zu verschaffen und die Erwartungen der Kunden zu erfüllen.
Mitarbeiterengagement steigern:
Lean-Prinzipien fördern das Engagement, die Problemlösung und die Befähigung der Mitarbeiter. Engagierte Mitarbeiter sind motivierter, was zu einem positiveren Arbeitsumfeld und kontinuierlicher Verbesserung führt.
Die 5 Prinzipien der Lean Manufacturing
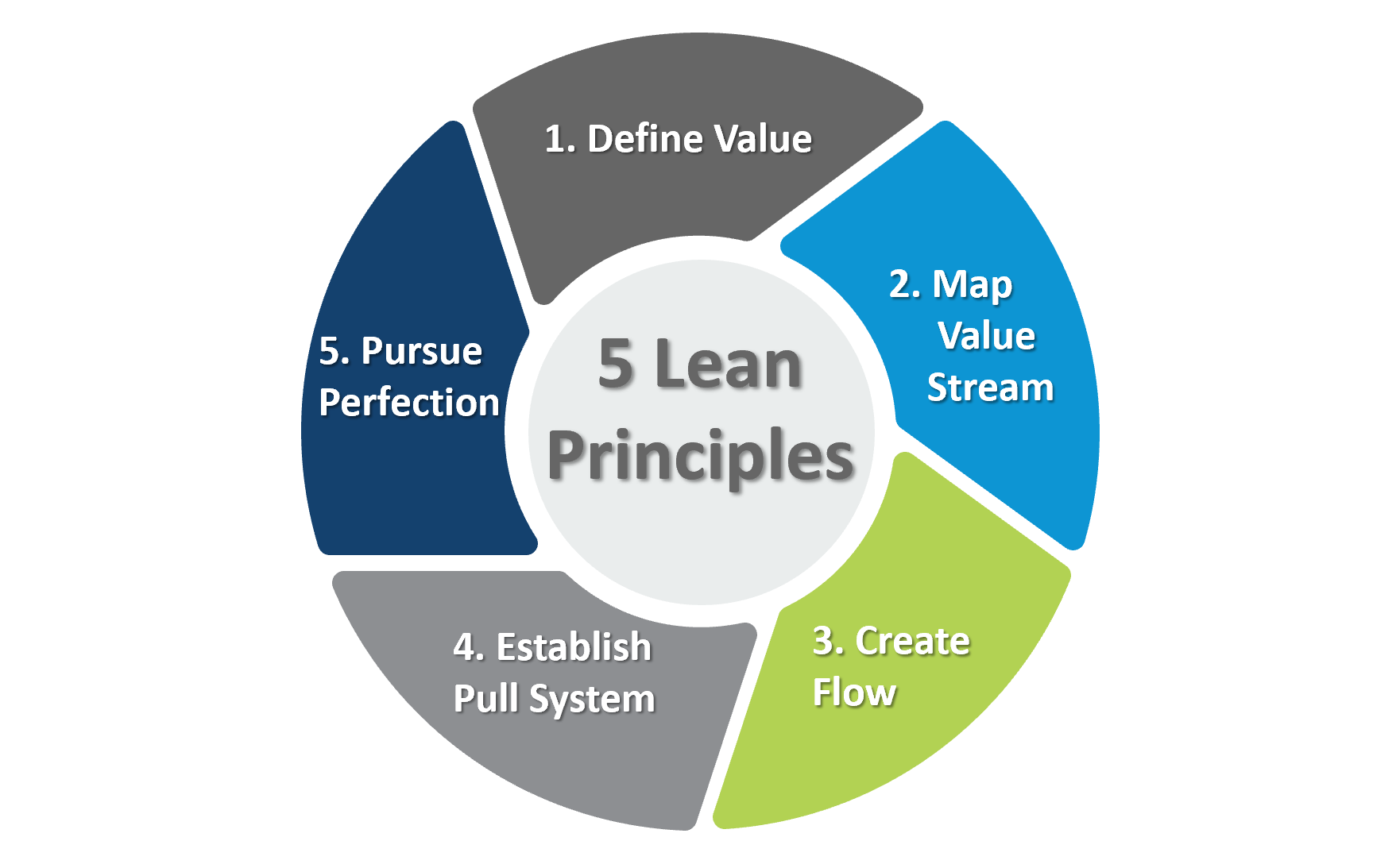

Was sind die 5 Prinzipien der Lean Manufacturing? Die fünf Grundprinzipien der Lean Manufacturing sind:
1/ Wert: Bereitstellung dessen, was für den Kunden wichtig ist
Das erste Prinzip von Lean Manufacturing besteht darin, „Wert“ zu verstehen und zu liefern. Bei diesem Konzept geht es darum, klar zu erkennen, was Kunden an einem Produkt oder einer Dienstleistung wirklich schätzen. Lean betrachtet den Wert kundenzentriert, um bestimmte Merkmale, Qualitäten oder Attribute zu identifizieren, für die Kunden bereit sind zu zahlen. Alles, was nicht zu diesen wertvollen Elementen beiträgt, gilt als Verschwendung.
Um „Wert“ zu schaffen, müssen die Aktivitäten eines Unternehmens eng an den Erwartungen und Bedürfnissen der Kunden ausgerichtet werden. Wenn ein Unternehmen versteht, was die Kunden wirklich wollen, kann es seine Ressourcen und Anstrengungen darauf ausrichten, genau das zu liefern, was Mehrwert schafft, und gleichzeitig Komponenten minimieren oder eliminieren, die keinen Mehrwert schaffen. Dieser Ansatz stellt sicher, dass Ressourcen effizient zugewiesen werden, was ein wichtiger Aspekt der Prinzipien des Lean Manufacturing ist.
2/ Wertstrom-Mapping: Visualisierung des Arbeitsflusses
Das zweite Lean-Prinzip, „Value Stream Mapping“, spielt eine entscheidende Rolle dabei, Unternehmen dabei zu helfen, Verschwendung in ihren Prozessen zu identifizieren und zu beseitigen.
Beim Wertstrom-Mapping geht es darum, eine umfassende visuelle Darstellung des gesamten Prozesses zu erstellen, von der Herkunft der Rohstoffe bis zum Endprodukt oder der bereitgestellten Dienstleistung. Diese Visualisierung hilft dabei, die Abfolge der am Prozess beteiligten Aktivitäten zu verstehen.
Die Wertstromanalyse ist ein wichtiges Instrument zur Unterscheidung zwischen Aktivitäten, die einen Mehrwert für ein Produkt oder eine Dienstleistung schaffen, und solchen, die dies nicht tun. Nicht wertschöpfende Aktivitäten, oft als „Muda“ bezeichnet, können verschiedene Formen der Verschwendung umfassen, wie z. B. Überproduktion, überschüssige Lagerbestände, Wartezeiten und unnötige Verarbeitung.
Durch die Identifizierung und anschließende Beseitigung dieser Verschwendungsquellen können Unternehmen ihre Prozesse rationalisieren, Durchlaufzeiten verkürzen und die betriebliche Gesamteffizienz verbessern.
Hier ist ein Beispiel für die Wertstromanalyse, das Ihnen helfen kann, es besser zu verstehen:
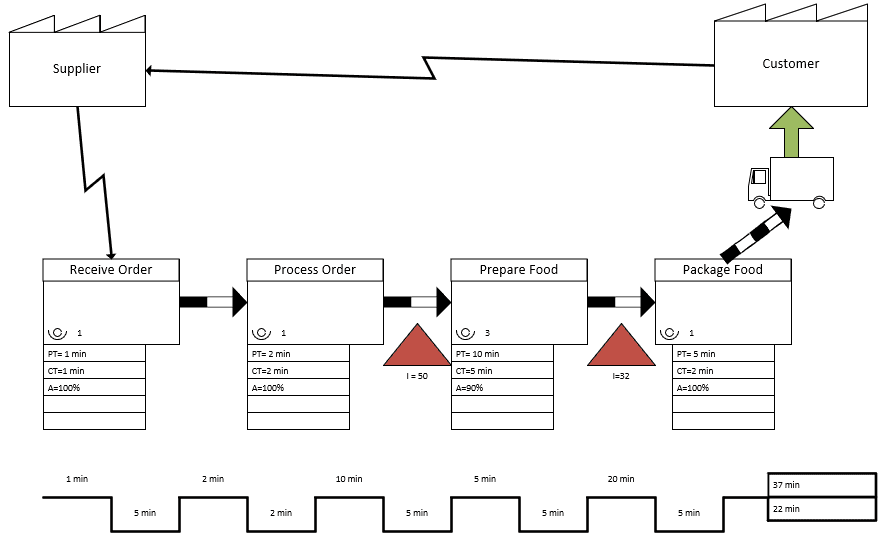

3/ Flow: Sicherstellung eines nahtlosen Fortschritts
„Flow“ soll einen reibungslosen und kontinuierlichen Arbeitsfluss innerhalb der Organisation schaffen. Das Flow-Konzept betont, dass die Arbeit ohne Unterbrechung oder Störung von einer Phase zur nächsten übergehen muss, was letztendlich die Effizienz fördert.
Aus organisatorischer Sicht fördert Lean die Schaffung einer Arbeitsumgebung, in der Aufgaben und Aktivitäten ohne Behinderung oder Verzögerung ablaufen.
Betrachten Sie ein Fertigungsband als Beispiel für die Erzielung eines „Flusses“. Jede Station führt eine bestimmte Aufgabe aus und die Produkte bewegen sich nahtlos und ohne Unterbrechung von einer Station zur anderen. Dies veranschaulicht das Konzept von Flow in Lean.
4/ Pull-System: Auf die Nachfrage reagieren
Beim Pull-System geht es um die Erstellung oder Bereitstellung von Dienstleistungen als Reaktion auf Kundenaufträge. Organisationen, die ein Pull-System einführen, stellen ihre Artikel nicht auf der Grundlage von Annahmen über die zukünftige Nachfrage her. Stattdessen reagieren sie auf tatsächlich eingegangene Bestellungen. Diese Praxis minimiert unter anderem die Überproduktion
Die sieben größten Abfallarten
in Lean Manufacturing.
Ein Beispiel für ein Pull-System ist ein Supermarkt. Kunden holen sich die Produkte, die sie benötigen, aus den Regalen, und der Supermarkt füllt die Regale nach Bedarf wieder auf. Dieses System stellt sicher, dass immer genügend Lagerbestände zur Deckung der Kundennachfrage vorhanden sind, es aber auch keine Überproduktion gibt.
Ein weiteres Beispiel für ein Pull-System ist ein Autohaus. Kunden holen die Autos, die sie interessieren, vom Parkplatz und machen damit eine Probefahrt. Das Autohaus bestellt beim Hersteller nur dann Neuwagen, wenn es zur Deckung der Kundennachfrage erforderlich ist.
5/ Kontinuierliche Verbesserung (Kaizen)
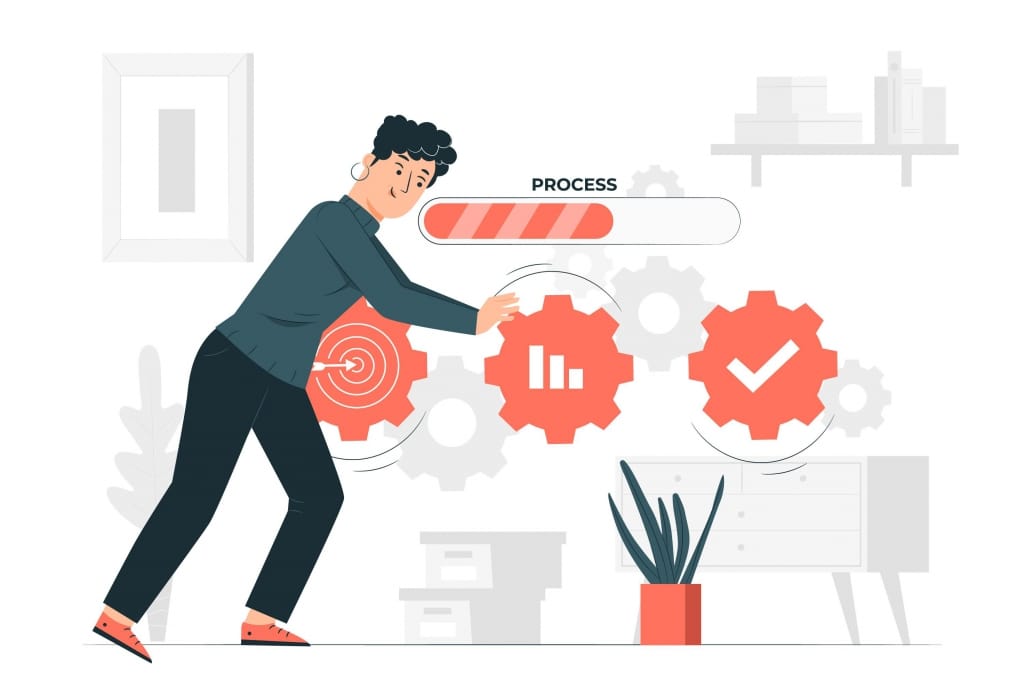

Das fünfte und letzte Lean-Prinzip ist die „Kontinuierliche Verbesserung“, auch bekannt als „Kaizen“ oder
Kontinuierlicher Kaizen-Verbesserungsprozess
. Es geht darum, eine Kultur der kontinuierlichen Verbesserung zu fördern.
Dabei geht es darum, im Laufe der Zeit kleine, kontinuierliche Verbesserungen vorzunehmen, anstatt radikale oder drastische Änderungen vorzunehmen. Diese kleinen Verbesserungen summieren sich und führen zu erheblichen Fortschritten bei Prozess, Qualität und Gesamteffizienz.
Einer der wichtigen Aspekte von Kaizen ist sein umfassender Charakter. Es fördert die Beteiligung aller Ebenen der Organisation und ermöglicht es den Mitarbeitern, ihre Ideen, Beobachtungen und Erkenntnisse einzubringen. Dieser Ansatz verbessert nicht nur die Problemlösungsfähigkeiten, sondern erhöht auch die Arbeitsmoral und das Engagement der Mitarbeiter.
Kaizen stellt sicher, dass die Organisation kontinuierlich motiviert ist, besser, effizienter und effektiver zu werden. Es ist eine Verpflichtung zur kontinuierlichen Verbesserung und ein grundlegender Aspekt einer Lean-Kultur.
Abschließende Überlegungen
Die 5 Prinzipien des Lean Manufacturing: Wert, Wertstrom-Mapping, Fluss, Pull-System und kontinuierliche Verbesserung (Kaizen) – bieten Unternehmen einen leistungsstarken Rahmen für die Erzielung betrieblicher Spitzenleistungen.
Unternehmen, die die L5-Prinzipien der Lean Manufacturing anwenden, verbessern nicht nur ihre Effizienz, sondern reduzieren auch Verschwendung und verbessern die Qualität ihrer Produkte und Dienstleistungen.
Häufigste Fragen
Was sind die 5 Prinzipien der Lean Manufacturing?
Die 5 Prinzipien der schlanken Fertigung sind Wert, Wertstrom-Mapping, Fluss, Pull-System und kontinuierliche Verbesserung (Kaizen).
Gibt es 5 oder 7 Lean-Prinzipien?
Obwohl es unterschiedliche Interpretationen gibt, sind die fünf oben genannten die am weitesten verbreiteten Lean-Prinzipien.
Was sind die 10 Regeln der Lean Production?
Die 10 Regeln der schlanken Produktion sind in der Regel kein Standardsatz in der schlanken Fertigung. Die Prinzipien der schlanken Produktion basieren in der Regel auf den zuvor genannten 5 Kernprinzipien. Einige Quellen listen möglicherweise „Regeln“ auf, aber diese sind nicht allgemein anerkannt.