Immagina un modo di fare le cose in cui nulla va sprecato, ogni passaggio rende il prodotto migliore e utilizzi tutte le tue risorse saggiamente. Questa è l'essenza della produzione snella. Se ti sei mai chiesto come alcune aziende riescano a produrre di più con meno, stai per scoprire i segreti. In questo blog post, esploreremo i 5 principi fondamentali della produzione snella, portandoti in un viaggio attraverso il modo in cui ha aiutato molte aziende in tutto il mondo.
Sommario
- Cos'è la produzione snella?
- Vantaggi della produzione snella
- I 5 principi della produzione snella
- Considerazioni finali
- Domande frequenti sui principi della produzione snella
Cos'è la produzione snella?
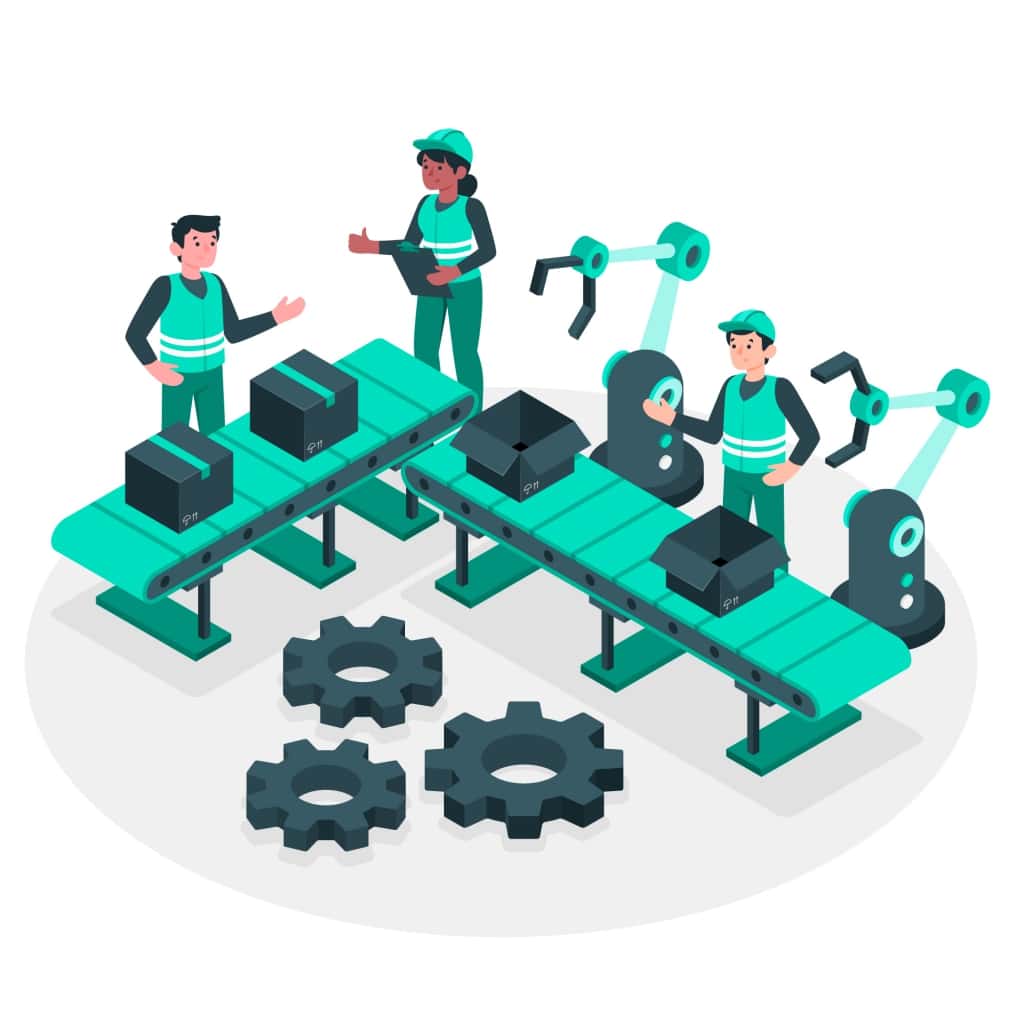
La produzione snella è un approccio sistematico alla produzione, che mira a ridurre gli sprechi, aumentare l’efficienza e fornire valore ai clienti. Questo approccio ha avuto origine da Sistema di produzione Toyota (TPS) ed è stato ora adottato in tutto il mondo da varie industrie e aziende.
L'obiettivo principale della produzione snella è semplificare il processo di produzione identificando ed eliminando attività, materiali o risorse non necessari che non contribuiscono direttamente al prodotto o servizio finale. Ciò aiuta a semplificare il processo e a renderlo più efficiente.
Vantaggi della produzione snella
La produzione snella offre numerosi vantaggi alle aziende che mirano a migliorare le proprie operazioni. Ecco cinque vantaggi chiave:
- Risparmio sui costi: La produzione snella identifica ed elimina gli sprechi nei processi, riducendo così i costi operativi. Ciò può includere costi di inventario inferiori, consumo energetico ridotto e meno rilavorazioni, con conseguente aumento dei profitti aziendali.
- Aumentare l'efficienza: Semplificando i processi, eliminando i colli di bottiglia e ottimizzando il flusso di lavoro, la produzione snella aumenta l'efficienza operativa. Ciò significa che le aziende possono produrre di più con la stessa quantità di risorse o meno, ottenendo il massimo dal proprio investimento.
- Qualità migliorata: La produzione snella si concentra sull’identificazione e sulla risoluzione delle cause profonde dei difetti, portando a una maggiore qualità del prodotto. Ciò significa meno errori, meno rilavorazioni e una migliore soddisfazione del cliente.
- Consegna più veloce: Le pratiche snelle portano a tempi di consegna più brevi e a una risposta più rapida alle esigenze dei clienti. La capacità di produrre e consegnare i prodotti in tempo può aiutare le aziende a ottenere un vantaggio competitivo e a soddisfare le aspettative dei clienti.
- Aumentare il coinvolgimento dei dipendenti: I principi Lean incoraggiano il coinvolgimento dei dipendenti, la risoluzione dei problemi e l’empowerment. I dipendenti coinvolti sono più motivati, il che si traduce in un ambiente di lavoro più positivo e in un miglioramento continuo.
I 5 principi della produzione snella
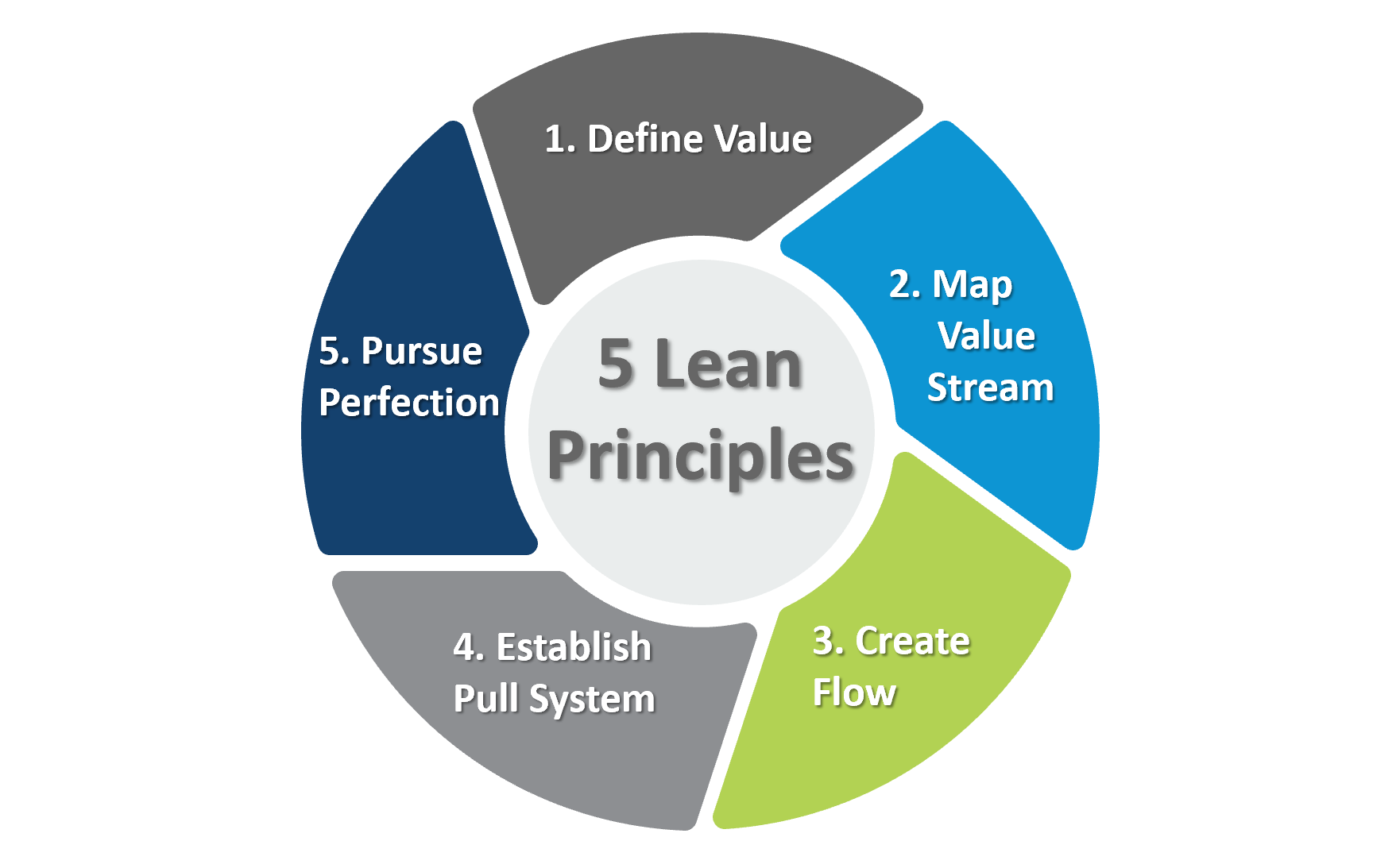
Quali sono i 5 principi della Lean Manufacturing? I cinque principi chiave della produzione snella sono:
1/ Valore: fornire ciò che conta per il cliente
Il primo principio della Lean Manufacturing è comprendere e fornire “valore”. Questo concetto ruota attorno all’identificazione chiara di ciò che i clienti apprezzano veramente in un prodotto o servizio. La visione del valore di Lean è incentrata sul cliente per identificare caratteristiche, qualità o attributi specifici per i quali i clienti sono disposti a pagare. Tutto ciò che non contribuisce a questi preziosi elementi è considerato rifiuto.
Realizzare “valore” implica allineare strettamente le attività di un'azienda con le aspettative e le esigenze dei clienti. Comprendendo ciò che realmente vogliono i clienti, un'organizzazione può indirizzare le proprie risorse e i propri sforzi verso la fornitura esattamente di ciò che aggiunge valore, riducendo al minimo o eliminando i componenti che non aggiungono valore. Questo approccio garantisce che le risorse siano allocate in modo efficiente, che è un aspetto chiave dei Principi di Lean Manufacturing.
2/ Mappatura del flusso di valore: visualizzare il flusso di lavoro
Il secondo principio Lean, "Value Stream Mapping", svolge un ruolo cruciale nell'aiutare le organizzazioni a identificare ed eliminare gli sprechi nei loro processi.
La mappatura del flusso di valore implica la creazione di una rappresentazione visiva completa dell’intero processo, dall’origine delle materie prime al prodotto finale o al servizio fornito. Questa visualizzazione aiuta a comprendere la sequenza delle attività coinvolte nel processo.
La mappatura del flusso di valore è uno strumento importante per distinguere tra le attività che apportano valore a un prodotto o servizio e quelle che non lo fanno. Le attività senza valore aggiunto, spesso denominate "muda", possono includere varie forme di spreco, come sovrapproduzione, inventario in eccesso, tempi di attesa e lavorazioni non necessarie.
Identificando ed eliminando queste fonti di spreco, le organizzazioni possono semplificare i propri processi, ridurre i tempi di consegna e migliorare l'efficienza operativa complessiva.
Ecco un esempio di Value Stream Mapping, che può aiutarti a capirlo meglio:
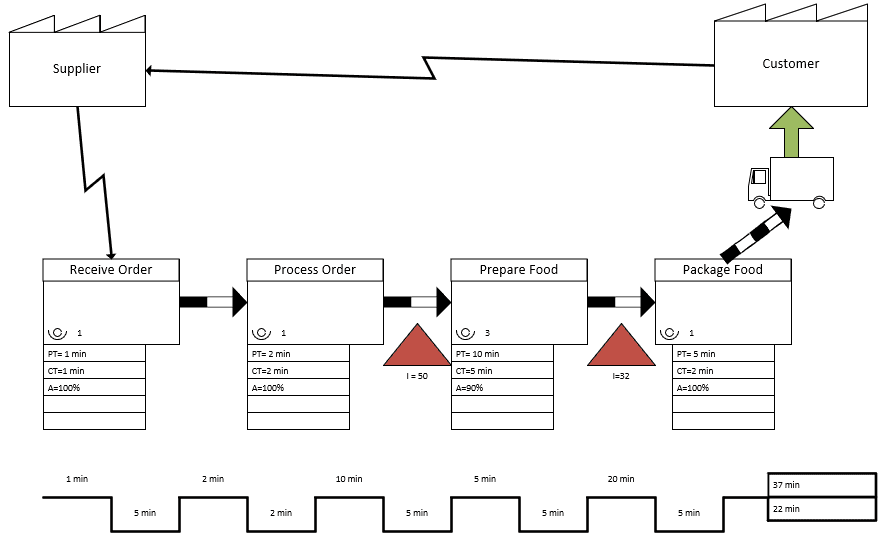
3/ Flusso: garantire una progressione senza interruzioni
Il "Flusso" ha lo scopo di creare un flusso di lavoro regolare e continuo all'interno dell'organizzazione. Il concetto di Flow sottolinea che il lavoro deve passare da una fase a quella successiva senza interruzioni o interruzioni, promuovendo in definitiva l’efficienza.
Da un punto di vista organizzativo, Lean incoraggia la creazione di un ambiente di lavoro in cui compiti e attività procedono senza ostacoli o ritardi.
Considera una catena di montaggio manifatturiera come un esempio di raggiungimento del “flusso”. Ciascuna stazione esegue un compito specifico e i prodotti si spostano senza soluzione di continuità da una stazione all'altra senza interruzioni. Questo illustra il concetto di Flow in Lean.
4/ Sistema Pull: rispondere alla domanda
Il sistema Pull riguarda la produzione o la fornitura di servizi in risposta agli ordini dei clienti. Le organizzazioni che adottano un sistema Pull non producono articoli sulla base di ipotesi di domanda futura. Rispondono invece agli ordini effettivi ricevuti. Questa pratica riduce al minimo la sovrapproduzione, uno dei le sette principali forme di rifiuti nella produzione snella.
- Un esempio di sistema pull è un supermercato. I clienti prelevano dagli scaffali i prodotti di cui hanno bisogno e il supermercato rifornisce gli scaffali secondo necessità. Questo sistema garantisce che vi siano sempre scorte sufficienti per soddisfare la domanda dei clienti, ma non vi è nemmeno sovrapproduzione.
- Un altro esempio di sistema pull è una concessionaria di automobili. I clienti ritirano dal parcheggio le auto a cui sono interessati e le portano a fare un giro di prova. La concessionaria ordina dal produttore solo auto nuove necessarie per soddisfare la domanda dei clienti.
5/ Miglioramento continuo (Kaizen)
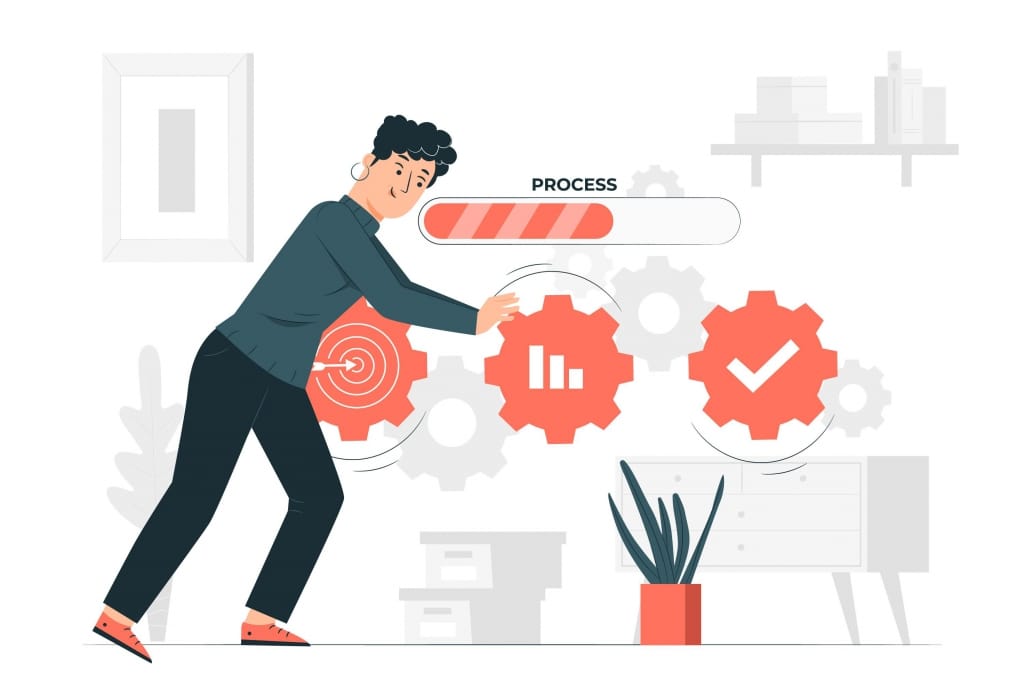
Il quinto e ultimo principio Lean è il “Miglioramento Continuo”, noto come “Kaizen” o Processo di miglioramento continuo Kaizen. Si tratta di promuovere una cultura del miglioramento continuo.
Si tratta di apportare miglioramenti piccoli e costanti nel tempo anziché apportare cambiamenti radicali o drastici. Questi piccoli miglioramenti si sommano, portando a progressi significativi nel processo, nella qualità e nell’efficienza complessiva.
Uno degli aspetti importanti di Kaizen è la sua natura globale. Incoraggia la partecipazione a tutti i livelli dell'organizzazione, consentendo ai dipendenti di contribuire con le proprie idee, osservazioni e intuizioni. Questo approccio non solo migliora le capacità di risoluzione dei problemi, ma aumenta anche il morale e il coinvolgimento dei dipendenti.
Kaizen garantisce che l'organizzazione sia continuamente motivata a diventare migliore, più efficiente e più efficace. È un impegno per il miglioramento continuo ed è un aspetto fondamentale di una cultura Lean.
Considerazioni finali
I 5 principi della produzione snella: valore, mappatura del flusso di valore, flusso, sistema pull e miglioramento continuo (Kaizen) - forniscono alle organizzazioni un potente quadro di riferimento per raggiungere l'eccellenza operativa.
Le organizzazioni che abbracciano i principi L5 della produzione snella non solo migliorano la propria efficienza, ma riducono anche gli sprechi e migliorano la qualità dei propri prodotti e servizi.
Domande frequenti
Quali sono i 5 principi della produzione snella?
I 5 principi della produzione snella sono valore, mappatura del flusso di valore, flusso, sistema pull e miglioramento continuo (Kaizen).
Esistono 5 o 7 principi snelli?
Sebbene esistano diverse interpretazioni, i principi Lean più ampiamente riconosciuti sono i 5 sopra menzionati.
Quali sono le 10 regole della produzione snella?
Le 10 regole della produzione snella in genere non sono uno standard stabilito nella produzione snella. I principi Lean si basano tipicamente sui 5 principi fondamentali menzionati in precedenza. Alcune fonti possono elencare "regole", ma non sono universalmente concordate.