Imaginez une façon de fabriquer des choses où rien ne se perd, où chaque étape améliore le produit et où vous utilisez toutes vos ressources à bon escient. C'est l'essence même de la production allégée. Si vous vous êtes déjà demandé comment certaines entreprises parviennent à produire plus avec moins, vous êtes sur le point de découvrir les secrets. blog poste, nous explorerons les 5 principes fondamentaux du Lean Manufacturing, vous emmenant dans un voyage à travers les méthodes qui ont aidé de nombreuses entreprises à travers le monde.
Table des matières
- Qu'est-ce que le Lean Manufacturing ?
- Avantages de la production allégée
- Les 5 principes du Lean Manufacturing
- Réflexions finales
- FAQ sur les principes du Lean Manufacturing
Qu'est-ce que le Lean Manufacturing ?
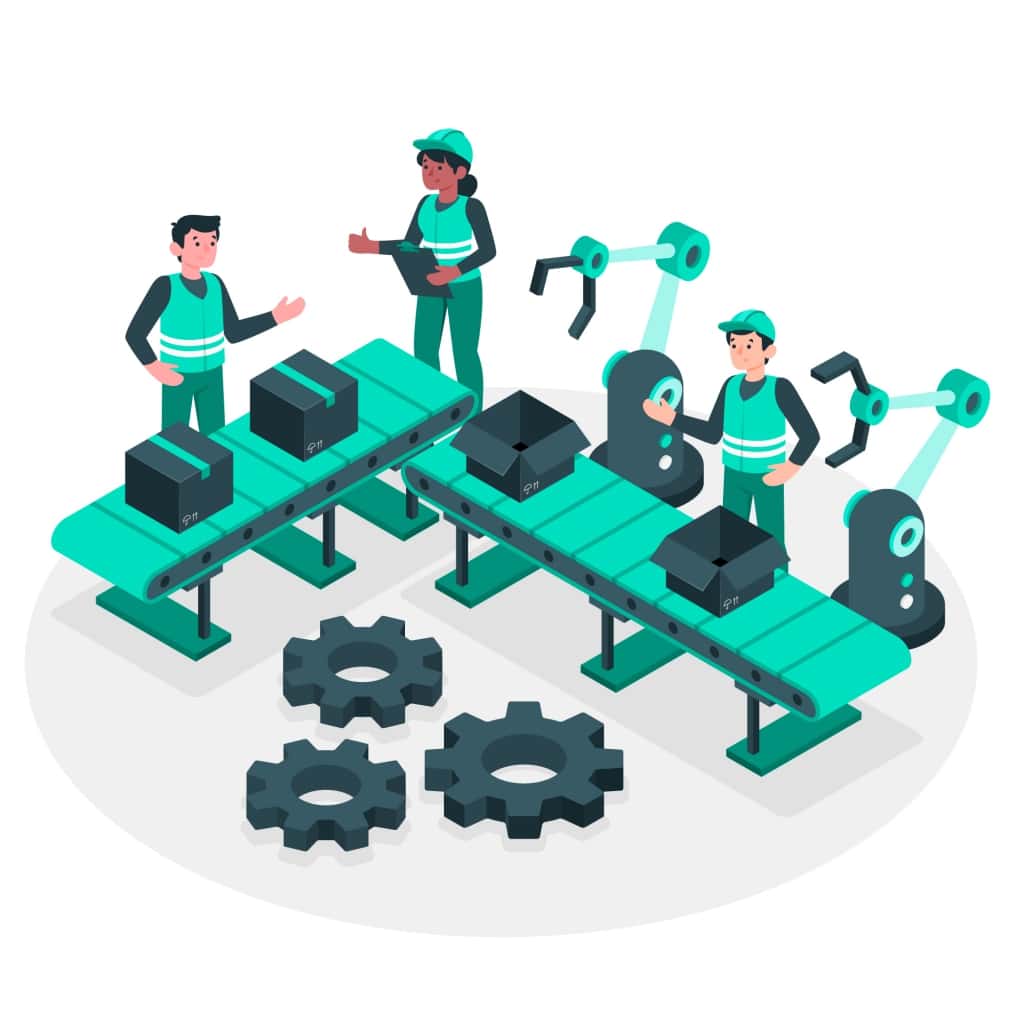
La production Lean est une approche systématique de la production, qui vise à réduire les déchets, à accroître l'efficacité et à apporter de la valeur aux clients. Cette approche est issue du Système de production Toyota (TPS) et a maintenant été adopté dans le monde entier par diverses industries et entreprises.
L'objectif principal de la production Lean est de simplifier le processus de production en identifiant et en supprimant toutes les activités, matériaux ou ressources inutiles qui ne contribuent pas directement au produit ou service final. Cela permet de rationaliser le processus et de le rendre plus efficace.
Avantages de la production allégée
Le Lean Manufacturing offre plusieurs avantages aux entreprises souhaitant améliorer leurs opérations. Voici cinq avantages clés :
- Les économies de coûts: Lean Manufacturing identifie et élimine les gaspillages dans les processus, réduisant ainsi les coûts d'exploitation. Cela peut inclure une baisse des coûts d’inventaire, une réduction de la consommation d’énergie et moins de retouches, augmentant ainsi les bénéfices de l’entreprise.
- Accroître l'efficacité: En rationalisant les processus, en éliminant les goulots d'étranglement et en optimisant le flux de travail, la production allégée augmente l'efficacité opérationnelle. Cela signifie que les entreprises peuvent produire davantage avec la même quantité de ressources ou moins, tirant ainsi le meilleur parti de leur investissement.
- Amélioration de la qualité: La fabrication Lean se concentre sur l’identification et la résolution des causes profondes des défauts, conduisant à une meilleure qualité des produits. Cela signifie moins d’erreurs, moins de retouches et une meilleure satisfaction client.
- Livraison plus rapide : Les pratiques Lean conduisent à des délais de livraison plus courts et à une réponse plus rapide aux besoins des clients. La capacité de produire et de livrer des produits à temps peut aider les entreprises à acquérir un avantage concurrentiel et à répondre aux attentes des clients.
- Augmentez l’engagement des employés : Les principes Lean encouragent l’engagement des employés, la résolution de problèmes et l’autonomisation. Les employés engagés sont plus motivés, ce qui conduit à un environnement de travail plus positif et à une amélioration continue.
Les 5 principes du Lean Manufacturing
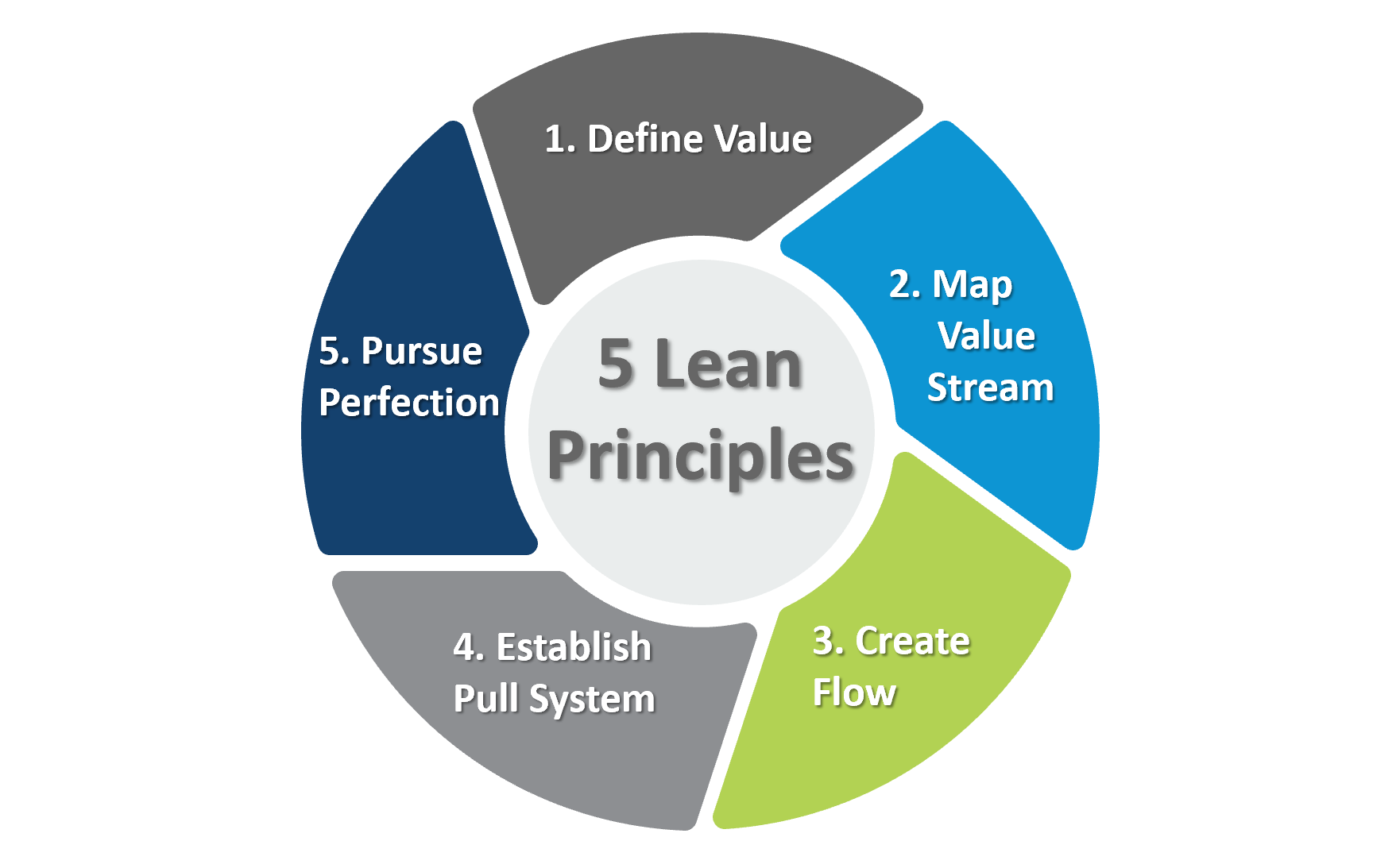
Quels sont les 5 principes du Lean Manufacturing ? Les cinq principes clés du Lean Manufacturing sont les suivants :
1/ Valeur : Fournir ce qui compte pour le client
Le premier principe du Lean Manufacturing est de comprendre et de fournir de la « valeur ». Ce concept consiste à identifier clairement ce que les clients apprécient réellement dans un produit ou un service. La vision Lean de la valeur est centrée sur le client pour identifier des caractéristiques, des qualités ou des attributs spécifiques pour lesquels les clients sont prêts à payer. Tout ce qui ne contribue pas à ces éléments précieux est considéré comme un déchet.
Réaliser de la « valeur » implique d'aligner étroitement les activités d'une entreprise sur les attentes et les besoins des clients. En comprenant ce que veulent réellement les clients, une organisation peut orienter ses ressources et ses efforts vers la fourniture exacte de ce qui ajoute de la valeur, tout en minimisant ou en éliminant les composants qui n'ajoutent pas de valeur. Cette approche garantit que les ressources sont allouées efficacement, ce qui est un aspect clé des principes du Lean Manufacturing.
2/ Cartographie de la chaîne de valeur : visualiser le flux de travail
Le deuxième principe Lean, « Value Stream Mapping », joue un rôle crucial en aidant les organisations à identifier et à éliminer le gaspillage dans leurs processus.
La cartographie de la chaîne de valeur implique la création d'une représentation visuelle complète de l'ensemble du processus, depuis l'origine des matières premières jusqu'au produit ou service final fourni. Cette visualisation aide à comprendre la séquence des activités impliquées dans le processus.
La cartographie de la chaîne de valeur est un outil important pour distinguer les activités qui contribuent à la valeur d'un produit ou d'un service et celles qui n'en apportent pas. Les activités sans valeur ajoutée, souvent appelées « muda », peuvent inclure diverses formes de gaspillage, telles que la surproduction, les stocks excédentaires, les délais d'attente et les transformations inutiles.
En identifiant puis en éliminant ces sources de gaspillage, les organisations peuvent rationaliser leurs processus, réduire les délais et améliorer l'efficacité opérationnelle globale.
Voici un exemple de Value Stream Mapping, qui peut vous aider à mieux la comprendre :
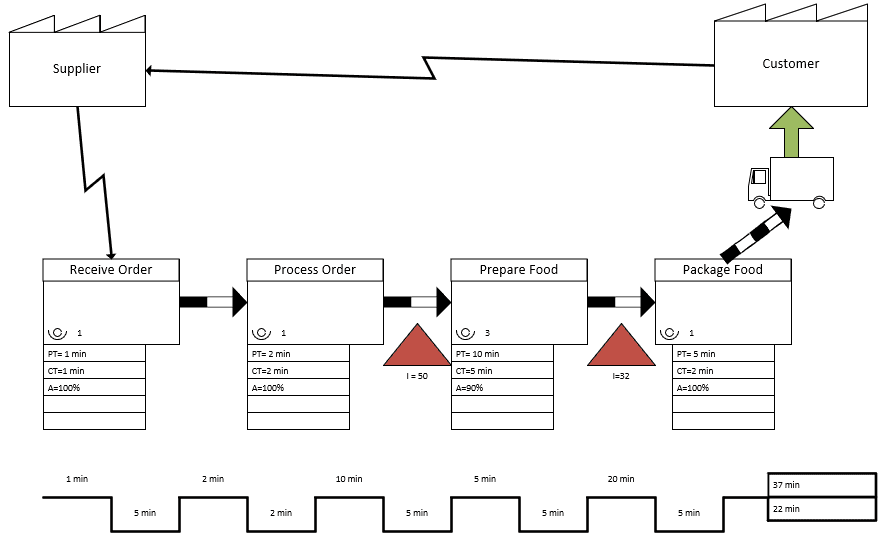
3/ Flow : assurer une progression fluide
« Flow » vise à créer un flux de travail fluide et continu au sein de l'organisation. Le concept de Flow souligne que le travail doit passer d'une étape à la suivante sans interruption ni perturbation, favorisant ainsi l'efficacité.
D'un point de vue organisationnel, Lean encourage l'établissement d'un environnement de travail où les tâches et les activités se déroulent sans entrave ni retard.
Considérons une chaîne de montage de fabrication comme exemple de réalisation du « flux ». Chaque station effectue une tâche spécifique et les produits se déplacent de manière transparente d'une station à l'autre, sans interruption. Cela illustre le concept de Flow dans le Lean.
4/ Pull System : Répondre à la demande
Le Pull System consiste à produire ou à fournir des services en réponse aux commandes des clients. Les organisations qui adoptent un système Pull ne fabriquent pas d'articles sur la base d'hypothèses de demande future. Au lieu de cela, ils répondent aux commandes réelles reçues. Cette pratique minimise la surproduction, l'une des les sept grandes formes de déchets en Lean Manufacturing.
- Un exemple de système pull est un supermarché. Les clients retirent des rayons les produits dont ils ont besoin et le supermarché réapprovisionne les rayons selon les besoins. Ce système garantit qu’il y a toujours suffisamment de stocks pour répondre à la demande des clients, mais qu’il n’y a pas non plus de surproduction.
- Un autre exemple de système pull est celui d’un concessionnaire automobile. Les clients retirent du parking les voitures qui les intéressent et les emmènent faire un essai routier. Le concessionnaire commande uniquement des voitures neuves au constructeur si nécessaire pour répondre à la demande des clients.
5/ Amélioration Continue (Kaizen)
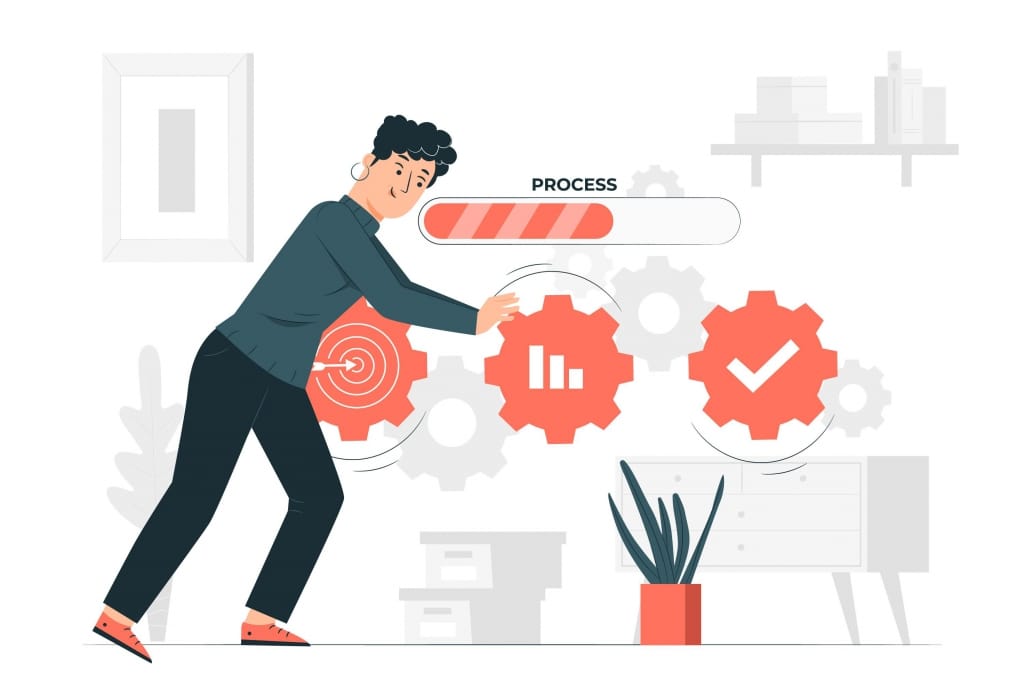
Le cinquième et dernier principe Lean est « l’amélioration continue », connu sous le nom de « Kaizen » ou Processus d'amélioration continue Kaizen. Il s’agit de favoriser une culture d’amélioration continue.
Cela implique d’apporter de petites améliorations cohérentes au fil du temps plutôt que d’apporter des changements radicaux ou drastiques. Ces petites améliorations s'additionnent, conduisant à des progrès significatifs en matière de processus, de qualité et d'efficacité globale.
L’un des aspects importants du Kaizen est sa nature globale. Il encourage la participation à tous les niveaux de l'organisation, permettant aux employés d'apporter leurs idées, leurs observations et leurs idées. Cette approche améliore non seulement les capacités de résolution de problèmes, mais augmente également le moral et l'engagement des employés.
Kaizen garantit que l'organisation est continuellement motivée à devenir meilleure, plus efficiente et plus efficace. Il s’agit d’un engagement envers l’amélioration continue et constitue un aspect fondamental d’une culture Lean.
Réflexions finales
Les 5 principes du Lean Manufacturing : valeur, cartographie de la chaîne de valeur, flux, système pull et amélioration continue (Kaizen) - fournissent aux organisations un cadre puissant pour atteindre l'excellence opérationnelle.
Les organisations qui adoptent les principes L5 du Lean Manufacturing améliorent non seulement leur efficacité, mais réduisent également les déchets et améliorent la qualité de leurs produits et services.
Foire aux questions (FAQ)
Quels sont les 5 principes du Lean Manufacturing ?
Les 5 principes du Lean Manufacturing sont la valeur, la cartographie de la chaîne de valeur, le flux, le système pull et l'amélioration continue (Kaizen).
Existe-t-il 5 ou 7 principes Lean ?
Bien qu’il existe différentes interprétations, les principes Lean les plus largement reconnus sont les cinq principes mentionnés ci-dessus.
Quelles sont les 10 règles de la production au plus juste ?
Les 10 règles de la production Lean ne constituent généralement pas une norme établie dans le cadre de la fabrication Lean. Les principes Lean reposent généralement sur les 5 principes fondamentaux mentionnés précédemment. Certaines sources peuvent énumérer des « règles », mais elles ne sont pas universellement acceptées.