In the dynamic landscape of organizational success, the key lies in continuous improvement methodologies. Whether you're steering a small team or overseeing a large corporation, the pursuit of excellence never rests. In this blog post, we'll explore the 5 continuous improvement methodologies, and 8 continuous improvement tools to unlock the secrets to fostering innovation, efficiency, and lasting success within your organization.
Table Of Contents
- What Is Continuous Improvement?
- 5 Continuous Improvement Methodologies
- 8 Essential Tools For Continuous Improvement
- Key Takeaways
- FAQs
What Is Continuous Improvement?
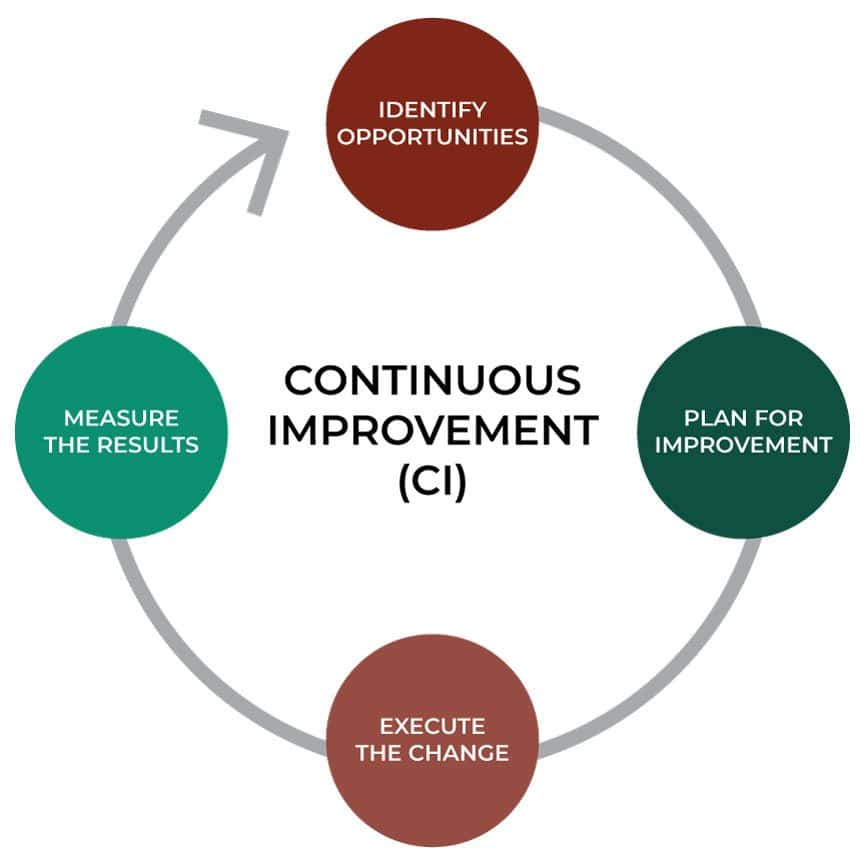
Continuous improvement is a systematic and ongoing effort to enhance processes, products, or services within an organization. It's a philosophy that embraces the idea that there is always room for improvement and seeks to make incremental changes to achieve excellence over time.
At its core, continuous improvement involves:
- Identifying Opportunities: Recognizing areas that can be improved, whether it's in workflow efficiency, product quality, or customer satisfaction.
- Making Changes: Implementing small, gradual changes rather than waiting for major overhauls. These changes are often based on data, feedback, or insights gathered from the organization's operations.
- Measuring Impact: Assessing the effects of the changes to determine their success and understand how they contribute to the overall improvement goals.
- Adapting and Learning: Embracing a culture of learning and adaptability. Continuous improvement acknowledges that the business environment is dynamic, and what works today may need adjustment tomorrow.
Continuous improvement is not a one-time project but a long-term commitment to excellence. It can take various forms, such as Lean methodologies, Six Sigma practices, or Kaizen principles, each providing a structured approach to achieving ongoing improvement. Ultimately, it's about fostering a mindset of innovation, efficiency, and a relentless pursuit of becoming better at what an organization does.
5 Continuous Improvement Methodologies
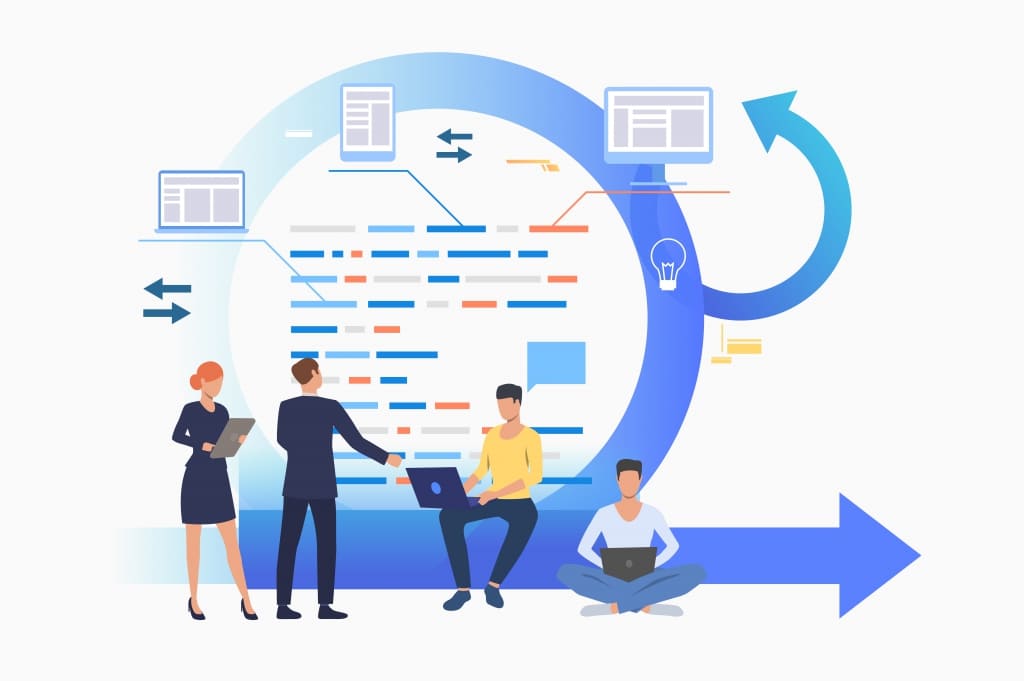
Here are five continuous improvement methodologies widely used in various industries:
1/ Kaizen - Continuous Improvement Methodologies
Kaizen Continuous Improvement Process, or Kaizen, a Japanese term meaning "change for the better," is a continuous improvement process that revolves around making small, incremental changes. It fosters a culture of constant improvement by encouraging employees at all levels to contribute ideas for enhancing processes, products, or services.
2/ Lean Manufacturing - Continuous Improvement Methodologies
The principles of Lean Manufacturing aim to streamline operations by minimizing waste, ensuring a continuous flow of work, and focusing on delivering value to the customer. Waste reduction, efficient processes, and customer satisfaction are at the core of this methodology.
3/ DMAIC Model - Continuous Improvement Methodologies
DMAIC Model (Define, Measure, Analyze, Improve, Control) is a structured approach within the Six Sigma methodology. It involves:
- Define: Clearly defining the problem or improvement opportunity.
- Measure: Quantifying the current state and establishing baseline metrics.
- Analyze: Investigating the root causes of the problem.
- Improve: Implementing solutions and enhancements.
- Control: Ensuring that the improvements are sustained over time.
4/ Theory of Constraints - Continuous Improvement Methodologies
What is the Theory of Constraints? Theory of Constraints (TOC) focuses on identifying and addressing the most significant limiting factor (constraint) within a system. By systematically improving or removing constraints, organizations can enhance the overall efficiency and productivity of the entire system.
5/ Hoshin Kanri - Continuous Improvement Methodologies
Hoshin Kanri planning is a strategic planning methodology originating from Japan. It involves aligning an organization's objectives and goals with its daily activities. Through a structured process, Hoshin Kanri ensures that everyone in the organization is working towards common objectives, fostering a cohesive and goal-oriented work environment.
8 Essential Tools For Continuous Improvement
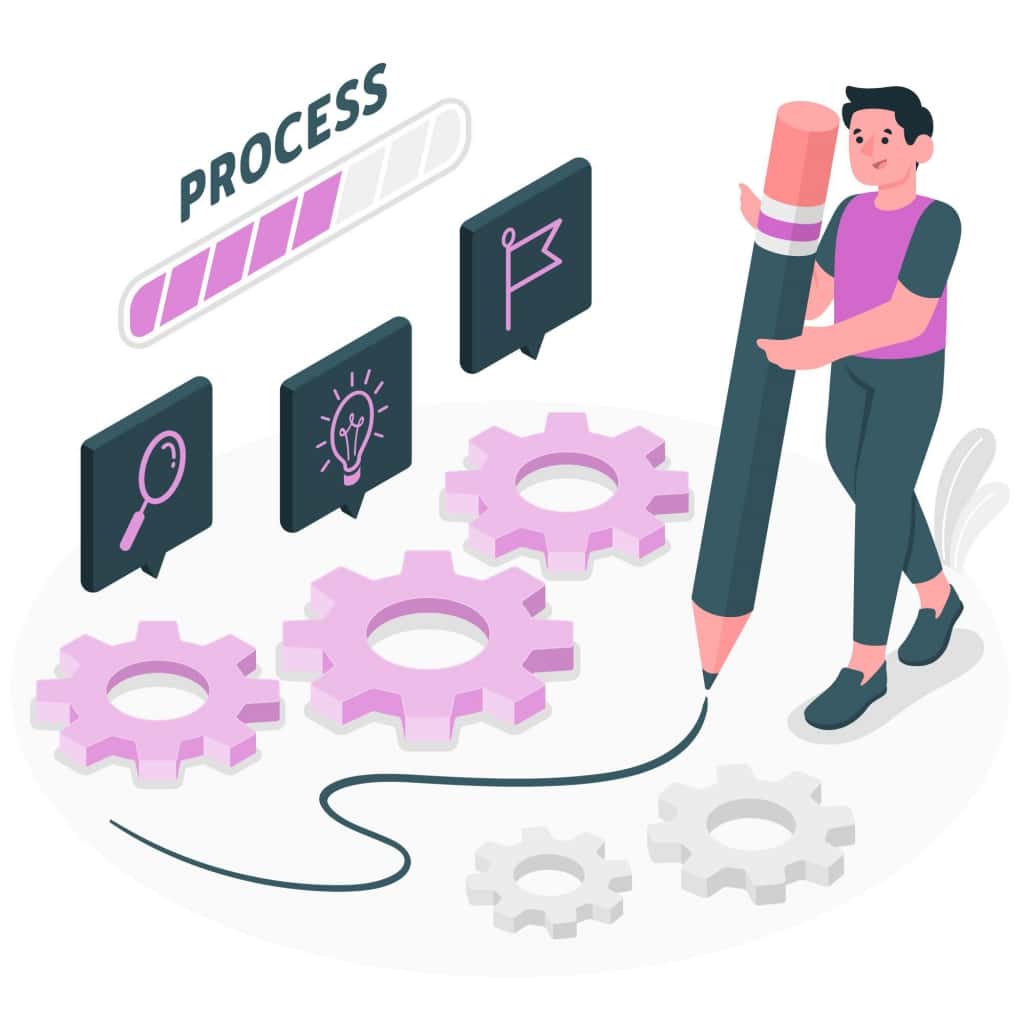
Explore the arsenal of Continuous Improvement Tools at your fingertips, ready to refine and elevate your processes.
1/ Value Stream Mapping
Value Stream Mapping is a tool that involves creating visual representations to analyze and improve workflows. By mapping out the entire process from start to finish, organizations can identify inefficiencies, reduce waste, and optimize the flow of work, ultimately enhancing overall productivity.
2/ Gemba Walks
What is Gemba walks? Gemba walks involve going to the actual workplace, or "Gemba," to observe, learn, and understand the real conditions of the processes. This hands-on approach allows leaders and teams to gain insights, identify improvement opportunities, and foster a culture of continuous improvement by directly engaging with the people involved in the work.
3/ PDCA Cycle (Plan, Do, Check, Act)
The PDCA cycle is an essential tool for achieving continuous improvement. It helps individuals and organizations to identify problems through of four stages:
- Plan: Identifying the problem and planning the improvement.
- Do: It's a good idea to start by testing out the plan on a small scale.
- Check: Assessing the results and analyzing data.
- Act: Taking action based on the results, whether to standardize the improvement, adjust the plan, or scale it up.
This cyclical process ensures a systematic and iterative approach to improvement.
4/ Kanban
Kanban is a visual management system that helps manage workflows efficiently. It involves using cards or visual signals to represent tasks or items moving through different stages of a process. Kanban provides a clear visual representation of work, reduces bottlenecks, and enhances the overall flow of tasks within a system.
5/ Six Sigma DMAIC
The 6 Sigma DMAIC methodology is a structured approach to process improvement. To ensure that a project runs smoothly, it's important to follow a structured approach.
This involves
- Defining the problem and project goals,
- Quantifying the current state and establishing baseline metrics,
- Investigating the root causes of the problem,
- Implementing solutions and enhancements,
- Ensuring that the improvements are sustained over time, maintaining consistent quality.
6/ Root Cause Analysis
Root Cause Analysis method is a tool that focuses on identifying and addressing the underlying causes of problems rather than just treating symptoms. By getting to the root of an issue, organizations can implement more effective and lasting solutions, preventing recurrence and promoting continuous improvement.
Paired with the simplicity of Root Cause Analysis Template, this tool offers organized frameworks for investigating issues. This helps organizations take a step-by-step approach to solving problems, encouraging a culture of continuous improvement.
7/ Five Whys
The Five Whys approach is a simple but powerful technique for digging deep into the root causes of a problem. It involves asking "Why" repeatedly (typically five times) until the core issue is identified. This method helps uncover the underlying factors contributing to a problem, facilitating targeted solutions.
8/ Ishikawa Diagram
An Ishikawa Diagram, or Fishbone diagram, is a visual tool used for problem-solving. It illustrates the potential causes of a problem, categorizing them into branches resembling fishbones. This graphical representation helps teams identify and explore various factors contributing to an issue, making it easier to understand complex problems and devise effective solutions.
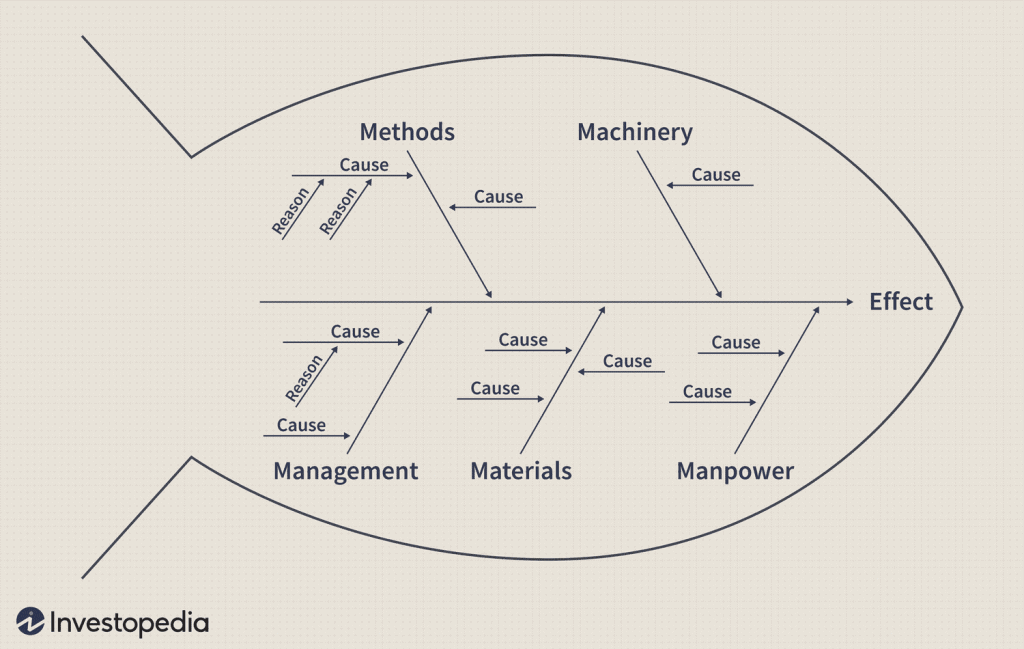
Key Takeaways
In wrapping up our exploration of Continuous Improvement Methodologies, we've uncovered the keys to organizational evolution. From Kaizen's small but impactful changes to the structured approach of Six Sigma, these Continuous Improvement methodologies shape the landscape of constant enhancement.
As you embark on your continuous improvement journey, don't forget to use AhaSlides. With AhaSlides’ interactive features and customizable design templates, AhaSlides becomes a valuable tool in fostering a culture of continuous improvement. Whether it's facilitating brainstorming sessions, mapping value streams, or conducting root cause analyses, AhaSlides offers a platform to make your continuous improvement initiatives not only effective but also engaging.
FAQs
What are the 4 stages of continuous improvement?
4 Stages of Continuous Improvement: Identify the Problem, Analyze the Current State, Develop Solutions. and Implement and Monitor
What are the Six Sigma continuous improvement methodologies?
Six Sigma Continuous Improvement Methodologies:
- DMAIC (Define, Measure, Analyze, Improve, Control)
- DMADV (Define, Measure, Analyze, Design, Verify)
What are the models of continuous improvement?
Models of Continuous Improvement: PDCA (Plan, Do, Check, Act), Theory of Constraints, Hoshin Kanri Planning.