Are you looking for a way to boost productivity, foster a culture of excellence, and enhance teamwork within your organization? Look no further than the Kaizen continuous improvement process.
In this blog post, we'll introduce you to the concept of the Kaizen Continuous Improvement Process and show you how it can empower your team or employees to reach new heights of success.
Table Of Contents
- What Is Kaizen Continuous Improvement?
- Why Is Continuous Process Improvement Important?
- 5 Principles Of Kaizen
- 6 Steps Of Kaizen Process
- Kaizen Continuous Improvement Examples
- Key Takeaways
- FAQs About Kaizen Continuous Improvement Process
What Is Kaizen Continuous Improvement?
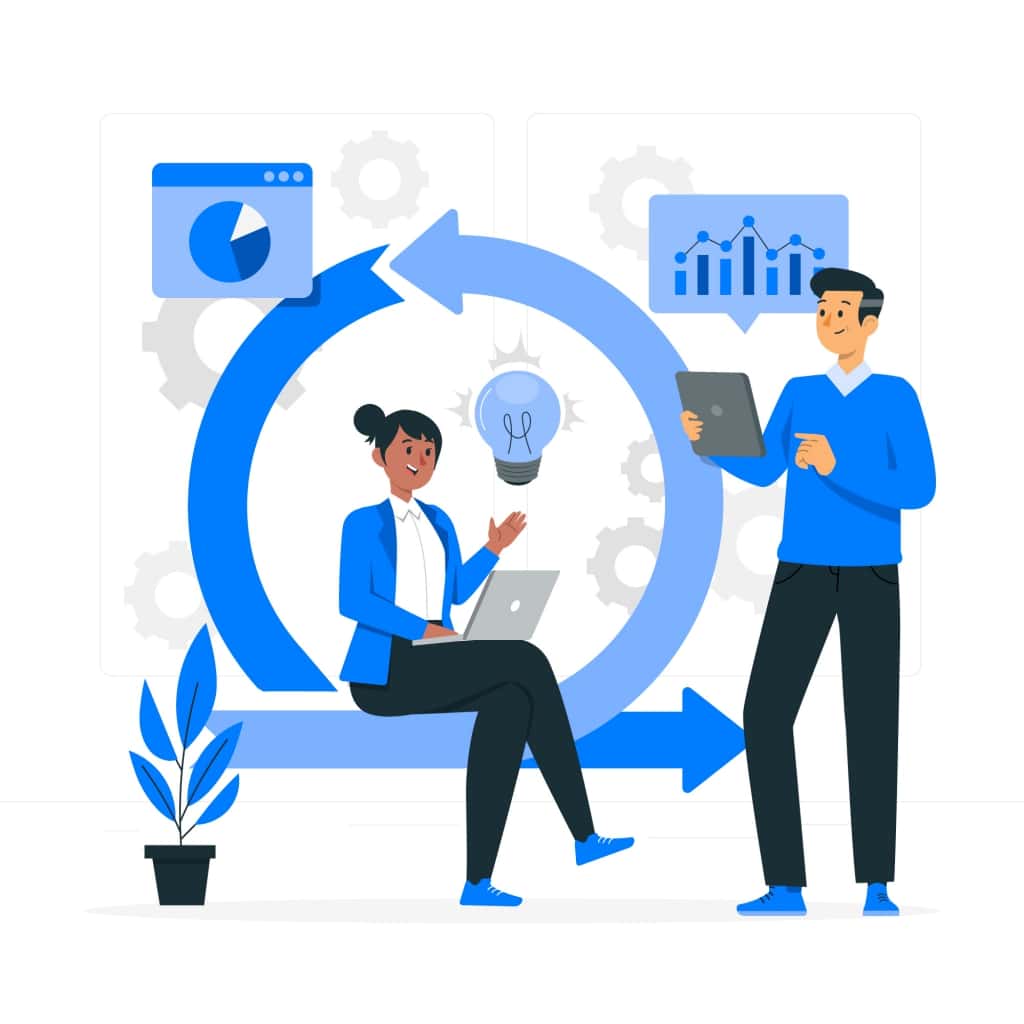
Kaizen Continuous Improvement, often referred to simply as "Kaizen," is a methodology that started in Japan and is widely used in various industries and organizations. Its goal is to achieve continuous and gradual improvements in processes, products, and operations. The term "Kaizen" translates to "change for the better" or "continuous improvement" in Japanese.
The Kaizen Continuous Improvement Process is a way of making things better by making small changes over time. Instead of big, sudden improvements, you keep making little adjustments to processes, products, or how you work. It's like taking tiny steps to reach a big goal.
This approach helps organizations and teams become more efficient, save money, and make their products or services even better.
Why Is Continuous Process Improvement Important?
Kaizen or Continuous Process Improvement is important for several reasons:
- Efficiency: It helps streamline processes, eliminate waste, and improve efficiency. This results in cost savings and a more productive use of resources.
- Quality: By continually making small improvements, organizations can enhance the quality of their products or services, leading to increased customer satisfaction and loyalty.
- Employee Engagement: It empowers employees by involving them in the improvement process. This engagement boosts morale, creativity, and a sense of ownership among team members.
- Innovation: Continuous improvement encourages innovation, as employees are encouraged to develop new and better ways of doing things.
- Adaptability: In today's fast-paced world, adaptability is crucial. Kaizen allows organizations to respond to changes and disruptions more effectively by fostering a culture of continuous learning and adjustment.
- Long-Term Growth: While big changes can be disruptive, Kaizen's small, incremental improvements are sustainable in the long run, contributing to an organization's overall growth and success.
5 Principles Of Kaizen
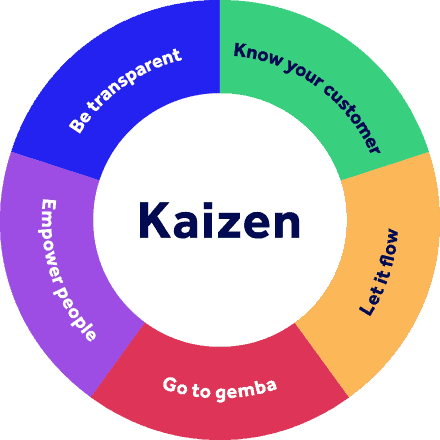
The five core principles of Kaizen/continuous improvement are:
- Know Your Customer: This means understanding the needs and expectations of your customers so that you can provide them with the best possible product or service.
- Let It Flow: This principle emphasizes the importance of creating smooth and efficient processes that minimize waste, reduce delays, and optimize workflow.
- Go to Gemba: "Gemba" is a Japanese term that means "the real place" or "the scene of the action." Go to where the work is happening to see how things are going. This way, you can find ways to make things better by watching and learning.
- Empower People: Kaizen relies on the participation of everyone in the organization. Everyone, from the boss to the workers, should have a say in how to make things better. Encourage people to come up with ideas and be part of the improvement.
- Be Transparent: Let everyone know what's happening with the improvements. It's a team effort, and being honest and clear helps everyone work together to improve things.
6 Steps Of Kaizen Process
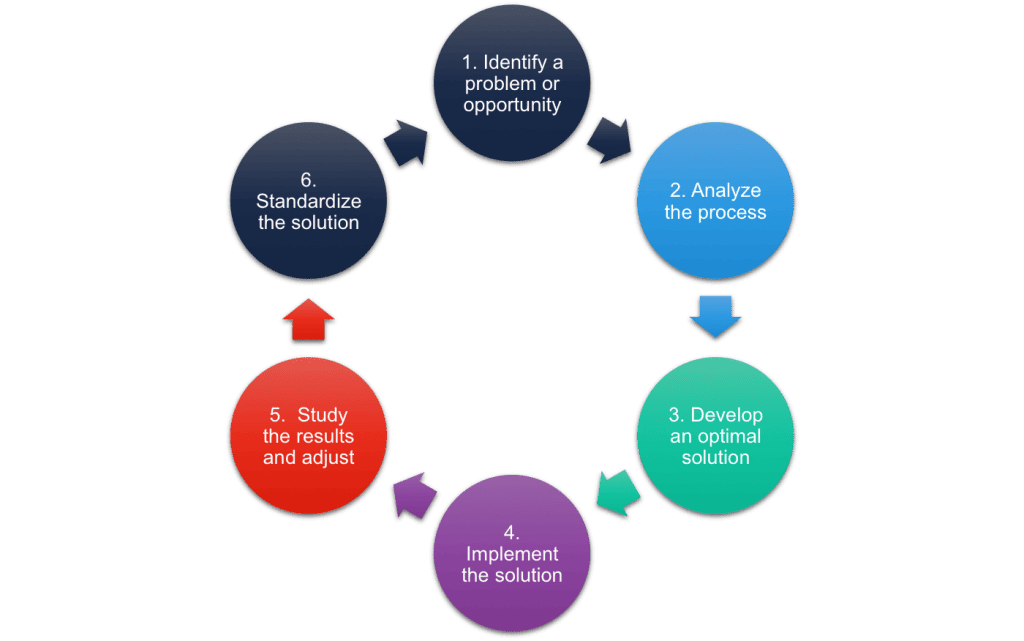
How to apply the Kaizen continuous improvement process for your organization? You can use The six steps of the Kaizen or the "Kaizen Cycle" as follows:
#1 - Identify the Problem
The first step is to identify a specific problem, area, or process within the organization that needs improvement. It could be efficiency, quality, customer satisfaction, or any other aspect that requires attention.
#2 - Plan for Improvement
Once your organization identifies the problem, create a plan to fix it. This plan includes setting clear goals, outlining the to-do actions, and establishing a timeline for implementation.
#3 - Implement Changes
The organization puts the plan into action by making small tweaks to see if they help or are effective. This allows them to see how well the improvements work.
#4 - Evaluate Results
After the changes have been implemented, the organization evaluates the results. Collect data and get feedback to see if the changes did what your organization wanted.
#5 - Standardize Improvements
If the changes work well, make them a permanent part of your organization's daily routines. This ensures that the improvements become a consistent and effective way of doing things.
#6 - Review and Repeat
The final step involves reviewing the entire process and its outcomes. It's also an opportunity to identify new areas for improvement. If needed, the Kaizen cycle can be repeated, starting with the first step, to address new issues or refine previous improvements.
The Kaizen continuous improvement process keeps your organization going in a circle, making things better all the time.
Kaizen Continuous Improvement Examples
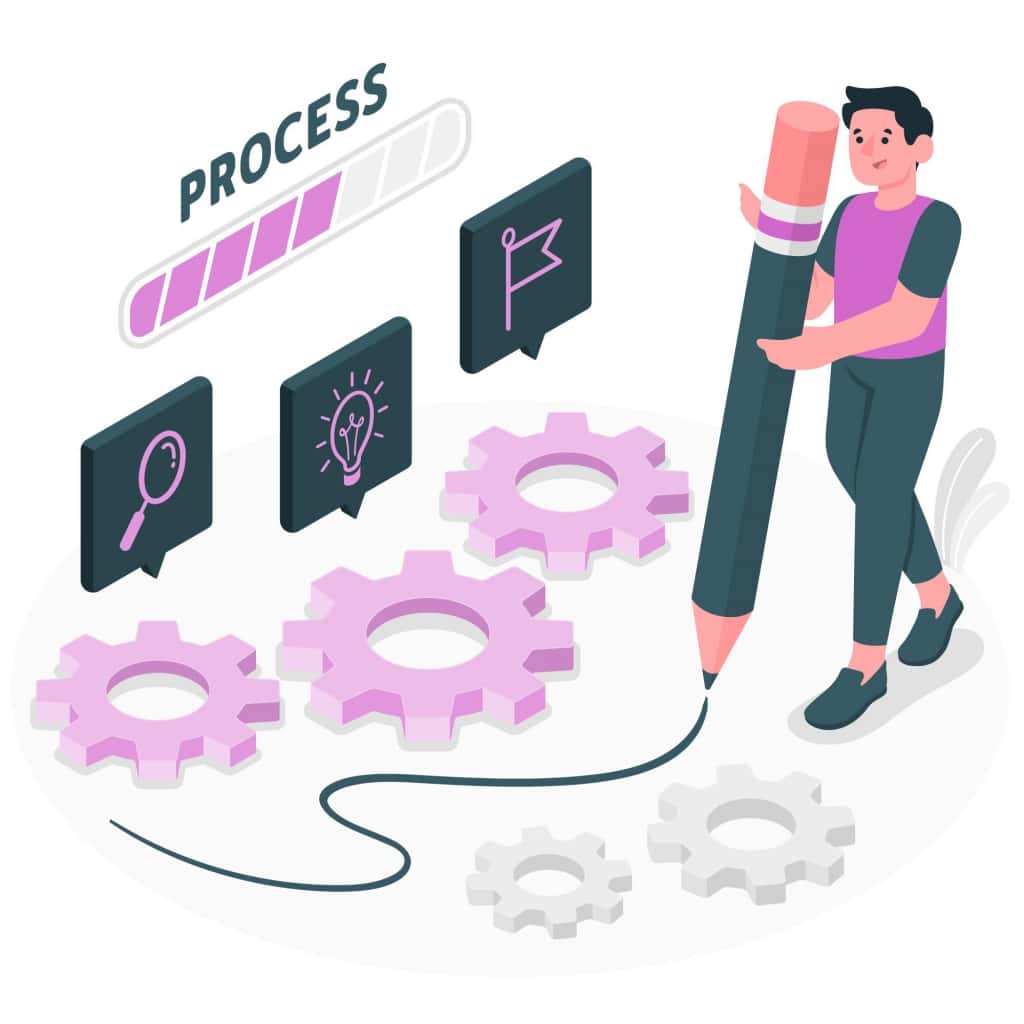
Here are some examples of how the Kaizen continuous improvement process can be applied in different areas of a business:
Kaizen Continuous Improvement Process in Marketing
- Identify the Problem: The marketing team notices a decline in website traffic and reduced engagement on social media.
- Plan for Improvement: The team plans to address the issue by improving content quality, optimizing SEO strategies, and enhancing social media posts.
- Implement Changes: They revamp website content, conduct keyword research, and create more engaging social media posts.
- Evaluate Results: They track website traffic, user engagement, and social media metrics to measure the impact of the changes.
- Standardize Improvements: The improved content and social media strategies become the new standard for ongoing marketing efforts.
- Review and Repeat: Regularly, the marketing team assesses website traffic and social media engagement to continue refining strategies for better results.
Kaizen Continuous Improvement Process in Customer Service
- Identify the Problem: Customers have been reporting long wait times for phone support and email responses.
- Plan for Improvement: The customer service team plans to reduce response times by implementing a more efficient email ticketing system and increasing staff during peak hours.
- Implement Changes: They introduce the new ticketing system and hire additional support staff during high-demand periods.
- Evaluate Results: The team monitors response times, customer feedback, and the resolution of support tickets.
- Standardize Improvements: The efficient ticketing system and staff allocation practices become the new standard for customer service operations.
- Review and Repeat: Regular reviews and customer feedback analysis ensure ongoing improvements in response times and customer satisfaction.
Related: Top 6 Continuous Improvement Examples in Business in 2025
Key Takeaways
The Kaizen continuous improvement process is a valuable approach for ongoing enhancements in your organization. To facilitate better meetings and presentations, utilize AhaSlides, a user-friendly platform that enhances collaboration and engagement. With Kaizen and AhaSlides, your organization can drive continuous progress and achieve its goals.
FAQs About Kaizen Continuous Improvement Process
What is Kaizen's continuous improvement?
Kaizen continuous improvement is a method of making small, incremental improvements in processes, products, and operations over time.
What are the 5 principles of kaizen?
The 5 principles of Kaizen are: 1 - Know Your Customer, 2 - Let It Flow, 3 - Go to Gemba, 4 - Empower People, 5 - Be Transparent
What are the 6 steps of the Kaizen process?
The 6 steps of the Kaizen process are: Identify the Problem, Plan for Improvement, Implement Changes, Evaluate Results, Standardize Improvements, Review and Repeat.
Ref: Tech Target | Study.com | The Learn Way