Picture a way of making things where nothing goes to waste, every step makes the product better, and you use all your resources wisely. That's the essence of lean manufacturing. If you've ever wondered how some companies manage to produce more with less, you're about to discover the secrets. In this blog post, we'll explore the 5 core principles of lean manufacturing, taking you on a journey through the way that has helped many businesses around the world.
Table Of Contents
- What Is Lean Manufacturing?
- Benefits Of Lean Manufacturing
- The 5 Principles Of Lean Manufacturing
- Final Thoughts
- FAQs About Principles Of Lean Manufacturing
What Is Lean Manufacturing?
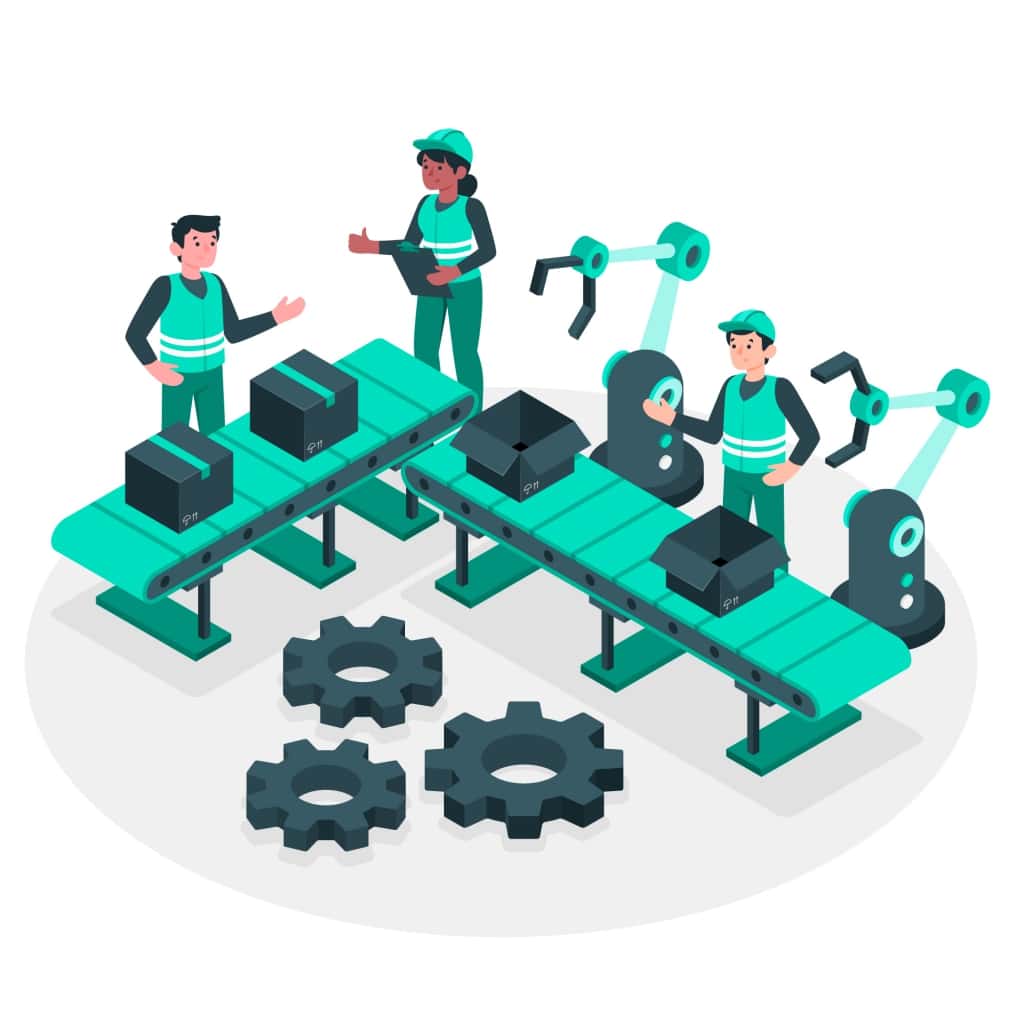
Lean manufacturing is a systematic approach to production, which aims to reduce waste, increase efficiency, and provide value to customers. This approach originated from the Toyota Production System (TPS) and has now been adopted worldwide by various industries and businesses.
The main goal of lean manufacturing is to simplify the production process by identifying and removing any unnecessary activities, materials, or resources that don't directly contribute to the final product or service. This helps to streamline the process and make it more efficient.
Benefits Of Lean Manufacturing
Lean manufacturing offers several benefits to companies aiming to improve their operations. Here are five key advantages:
- Cost savings: Lean manufacturing identifies and eliminates waste in processes, thereby reducing operating costs. This can include lower inventory costs, reduced energy consumption, and less rework, ultimately increasing company profits.
- Increase efficiency: By streamlining processes, eliminating bottlenecks, and optimizing workflow, lean manufacturing increases operational efficiency. This means businesses can produce more with the same amount of resources or less, getting the most out of their investment.
- Improved quality: Lean manufacturing focuses on identifying and resolving the root causes of defects, leading to higher product quality. This means fewer errors, less rework, and better customer satisfaction.
- Faster delivery: Lean practices lead to shorter lead times and faster response to customer needs. The ability to produce and deliver products on time can help companies gain a competitive advantage and meet customer expectations.
- Increase employee engagement: Lean principles encourage employee engagement, problem-solving, and empowerment. Engaged employees are more motivated, leading to a more positive work environment and continuous improvement.
The 5 Principles Of Lean Manufacturing
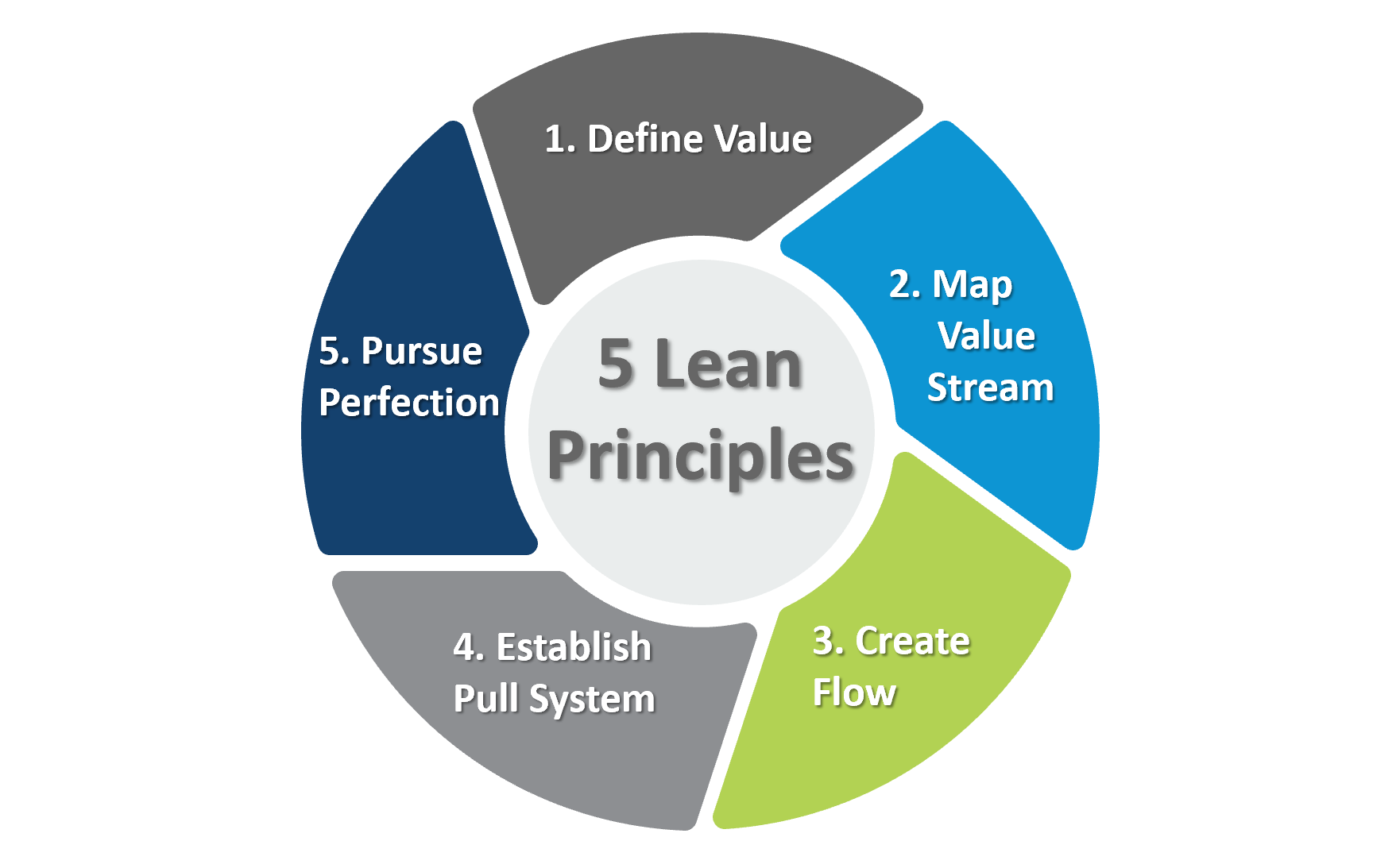
What are the 5 principles of Lean manufacturing? The five key principles of lean manufacturing are:
1/ Value: Providing What Matters to the Customer
The first principle of Lean Manufacturing is to understand and deliver “Value”. This concept revolves around clearly identifying what customers truly value in a product or service. Lean's view of value is customer-centric to identify specific features, qualities, or attributes for which customers are willing to pay. Anything that doesn't contribute to these valuable elements is considered waste.
Realizing “value” involves closely aligning a business's activities with customer expectations and needs. By understanding what customers really want, an organization can direct its resources and efforts toward delivering exactly what adds value, while minimizing or eliminating components that don't add value. This approach ensures that resources are allocated efficiently, which is a key aspect of Principles Of Lean Manufacturing.
2/ Value Stream Mapping: Visualizing the Flow of Work
The second Lean principle, "Value Stream Mapping," plays a crucial role in helping organizations identify and eliminate waste in their processes.
Value stream mapping entails creating a comprehensive visual representation of the entire process, from the origin of raw materials to the final product or service provided. This visualization aids in understanding the sequence of activities involved in the process.
Value stream mapping is an important tool for distinguishing between activities that contribute value to a product or service and those that do not. Non-value-adding activities, often referred to as "muda", can include various forms of waste, such as overproduction, excess inventory, waiting time, and unnecessary processing.
By identifying and then eliminating these sources of waste, organizations can streamline their processes, reduce lead times, and improve overall operational efficiency.
Here is an example of Value Stream Mapping, which can help you better understand it:
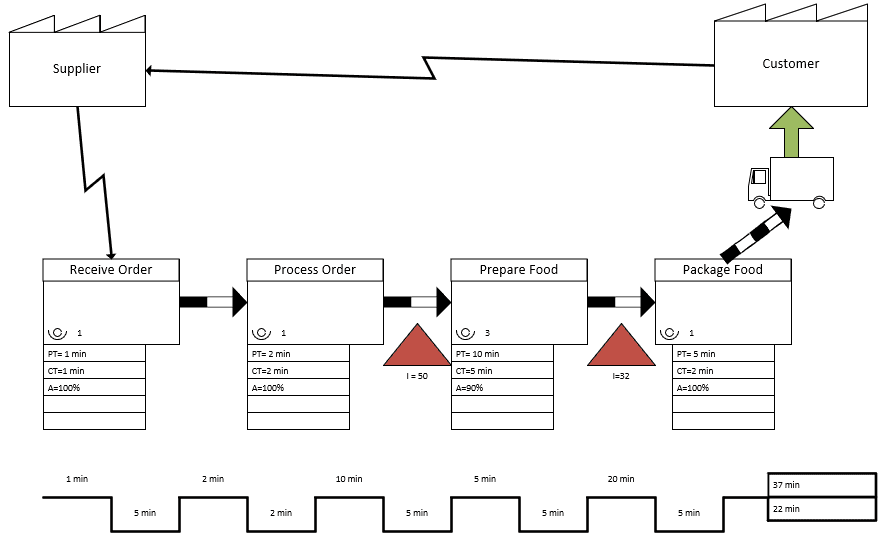
3/ Flow: Ensuring Seamless Progression
“Flow” is intended to create a smooth and continuous flow of work within the organization. The concept of Flow emphasizes that work must move from one stage to the next without interruption or disruption, ultimately promoting efficiency.
From an organizational perspective, Lean encourages establishing a work environment where tasks and activities proceed without hindrance or delay.
Consider a manufacturing assembly line as an example of achieving “flow.” Each station performs a specific task and products move seamlessly from one station to another without interruption. This illustrates the concept of Flow in Lean.
4/ Pull System: Responding to Demand
The Pull System is about producing or delivering services in response to customer orders. Organizations adopting a Pull System do not manufacture items based on assumptions of future demand. Instead, they respond to actual orders received. This practice minimizes overproduction, one of the seven major forms of waste in Lean manufacturing.
- An example of a pull system is a supermarket. Customers pull the products they need from the shelves, and the supermarket restocks the shelves as needed. This system ensures that there is always enough inventory to meet customer demand, but there is also no overproduction.
- Another example of a pull system is a car dealership. Customers pull the cars they are interested in off the lot and take them for a test drive. The dealership only orders new cars from the manufacturer as needed to meet customer demand.
5/ Continuous Improvement (Kaizen)
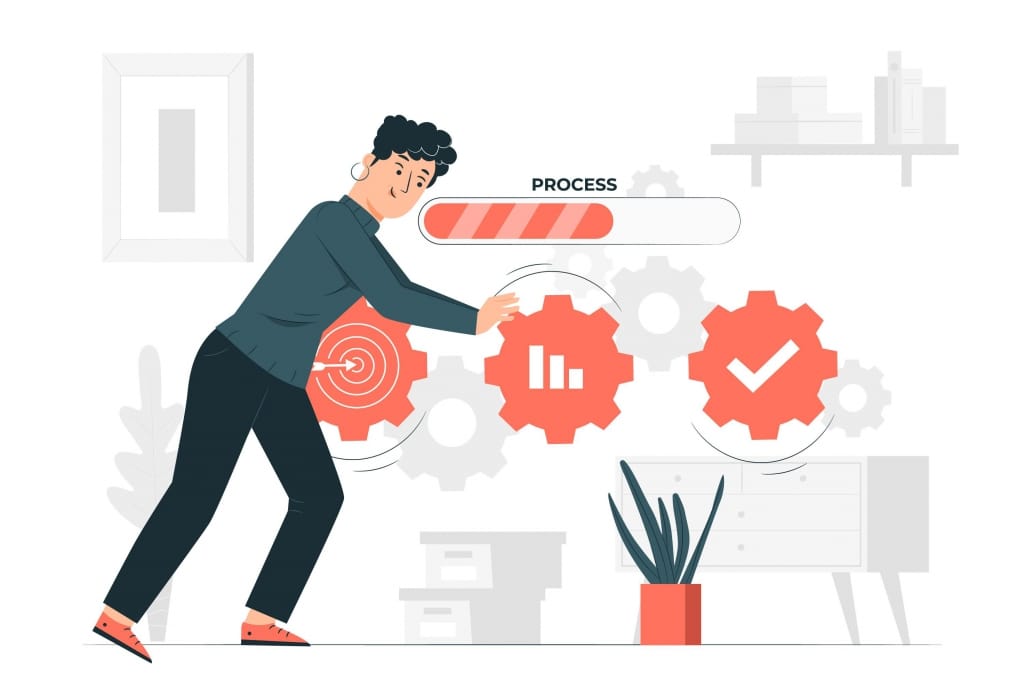
The fifth and final Lean principle is "Continuous Improvement," known as "Kaizen” or Kaizen continuous improvement process. It is about fostering a culture of ongoing improvement.
It involves making small, consistent improvements over time rather than making radical or drastic changes. These small improvements add up, leading to significant advances in process, quality, and overall efficiency.
One of the important aspects of Kaizen is its comprehensive nature. It encourages participation from every level of the organization, allowing employees to contribute their ideas, observations, and insights. This approach not only enhances problem-solving abilities but also increases employee morale and engagement.
Kaizen ensures that the organization is continuously motivated to become better, more efficient, and more effective. It is a commitment to continuous improvement and is a fundamental aspect of a Lean culture.
Final Thoughts
The 5 Principles Of Lean Manufacturing: Value, Value Stream Mapping, Flow, Pull System, and Continuous Improvement (Kaizen) - provide organizations with a powerful framework for achieving operational excellence.
Organizations that embrace L5 Principles Of Lean Manufacturing not only improve their efficiency but also reduce waste and enhance the quality of their products and services.
Frequently Asked Questions
What are the 5 principles of lean manufacturing?
The 5 principles of lean manufacturing are Value, Value Stream Mapping, Flow, Pull System, and Continuous Improvement (Kaizen).
Are there 5 or 7 lean principles?
While there are different interpretations, the most widely recognized Lean principles are the 5 mentioned above.
What are the 10 rules of lean production?
The 10 rules of lean production are typically not a standard set in Lean manufacturing. Lean principles are typically based on the 5 core principles mentioned earlier. Some sources may list "rules," but they are not universally agreed upon.