Imagine having a clear, bird's-eye view of your entire business process, from start to finish. Sounds too good to be true, right? Well, not if you've mastered the art of value stream mapping. In this blog post, we're going to explore the fundamentals of value stream mapping, its benefits, its examples, and how value stream mapping works.
Table Of Contents
- What Is Value Stream Mapping?
- Benefits Of Value Stream Mapping
- How Value Stream Mapping Works?
- Value Stream Mapping Symbols
- Value Stream Mapping Examples
- Final Thoughts
- FAQs
What Is Value Stream Mapping?
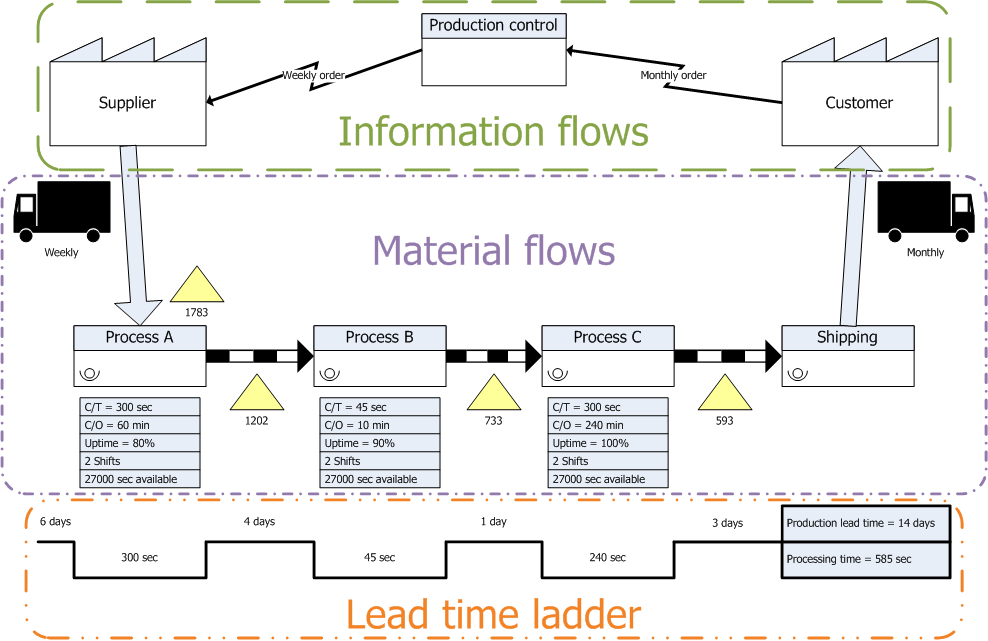
Value stream mapping (VSM) is a visual and analytical tool that helps organizations understand, improve, and optimize the flow of materials, information, and activities involved in delivering a product or service to customers.
VSM provides a clear and comprehensive overview of a process, identifying areas of waste, inefficiency, and opportunities for improvement. It is a powerful technique that can be applied to a wide range of industries and processes, including service-oriented businesses.
Benefits Of Value Stream Mapping
Here are five key benefits of Value Stream Mapping:
- Identifying Waste: Value Stream Mapping helps pinpoint areas of waste in an organization's processes, such as unnecessary steps, waiting times, or excess inventory. By recognizing these inefficiencies, they can work on reducing or eliminating them, saving time and resources.
- Increased Efficiency: It streamlines organizations’ processes, making them more efficient. This means their work gets done faster, which can lead to quicker delivery times and improved productivity.
- Improved Quality: Value Stream Mapping also focuses on quality control. It helps identify areas where defects or errors may occur and allows the implementation of measures to enhance quality and reduce errors.
- Cost Savings: By eliminating waste and improving efficiency, Value Stream Mapping can reduce operational costs, which is crucial for maintaining profitability.
- Enhanced Communication: It provides a visual representation of the processes, which can help employees easily understand. This promotes better communication and collaboration among employees, leading to smoother operations and a more effective work environment.
How Value Stream Mapping Works?
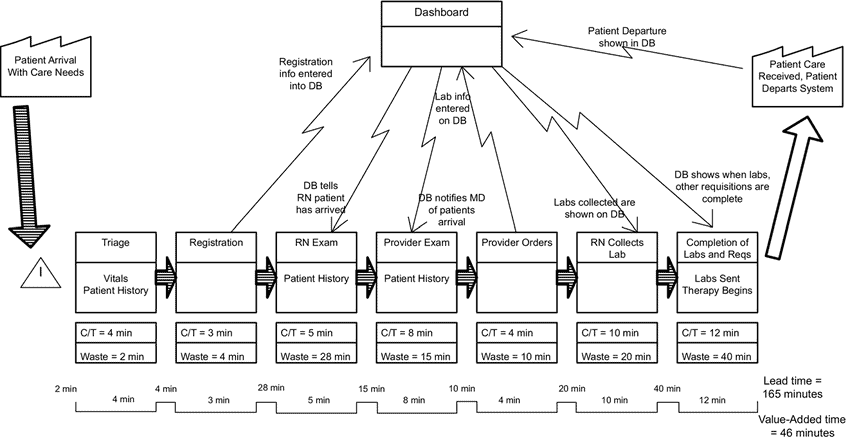
Value Stream Mapping works in organizations and businesses by providing a structured approach to understanding, analyzing, and improving processes. Here's how it typically works:
1/ Select the Process:
The first step is to choose a specific process within the organization that you want to examine and improve. This could be a manufacturing process, a service delivery process, or any other workflow.
2/ Start and End Points:
Figure out where the process begins (like receiving raw materials) and where it ends (like delivering the finished product to the customer).
3/ Map the Current State:
- The team creates a visual representation (the "current state map") of the process, showing all the steps involved.
- Within this map, it's important to distinguish between value-added and non-value-added steps.
- Value-added steps are those that directly contribute to transforming raw materials into a finished product or service that the customer is willing to pay for. These are the steps that add value to the final product.
- Non-value-added steps are those that are necessary for the process to function but do not directly contribute to the value that the customer is willing to pay for. These steps might include inspections, handovers, or waiting times.
- This map also includes symbols and labels to represent various elements like materials, information flow, and time.
4/ Identify Problems and Bottlenecks:
With the current state map in front of them, the team identifies and discusses problems, inefficiencies, bottlenecks, and any sources of waste within the process. This can include waiting times, excessive inventory, or redundant steps.
5/ Collect Data:
Data on cycle times, lead times, and inventory levels may be collected to quantify the issues and their impact on the process.
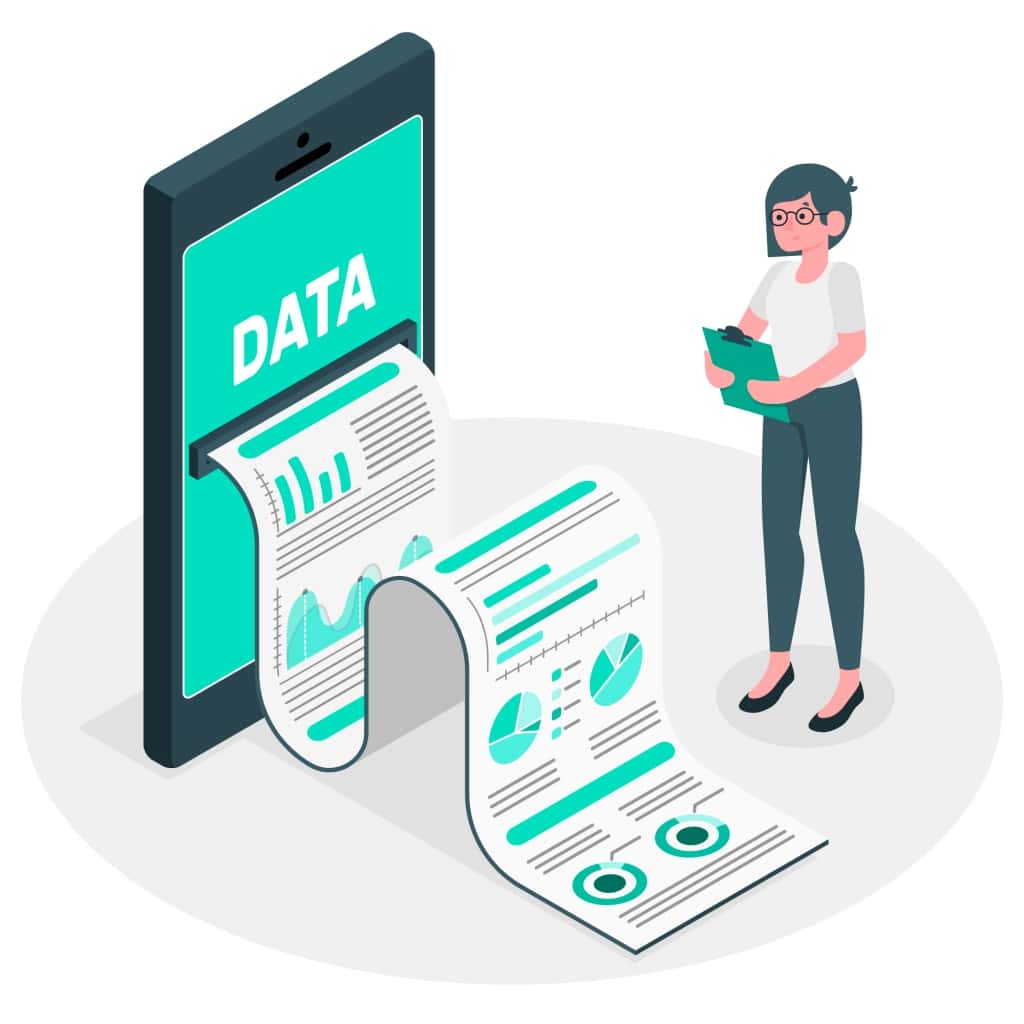
6/ Map the Future State:
- Based on the identified problems and inefficiencies, the team collaboratively creates a "future state map." This map represents how the process could work optimally and efficiently, with improvements incorporated.
- The future state map is a visual plan for making the process better.
7/ Implement Changes:
Organizations implement the improvements identified in the future state map. This can involve changes in processes, resource allocation, technology adoption, or other necessary adjustments.
8/ Monitor and Measure Progress:
Once changes are implemented, it's essential to monitor the process continually. Key performance metrics, such as cycle times, lead times, and customer satisfaction, are tracked to ensure that the improvements are effective.
9/ Continuous Improvement:
Value Stream Mapping encourages a culture of continuous improvement. Organizations regularly review and update their maps, looking for new opportunities to enhance processes and provide greater value to customers.
10/ Communication and Collaboration:
VSM promotes better communication and collaboration among team members as they work together to analyze, plan, and implement changes. It fosters a shared understanding of processes and their improvement.
Value Stream Mapping Symbols
Value Stream Mapping employs a set of symbols to visually represent different aspects of a process. These symbols serve as a visual language to simplify the understanding and analysis of the process. Some common VSM symbols include:
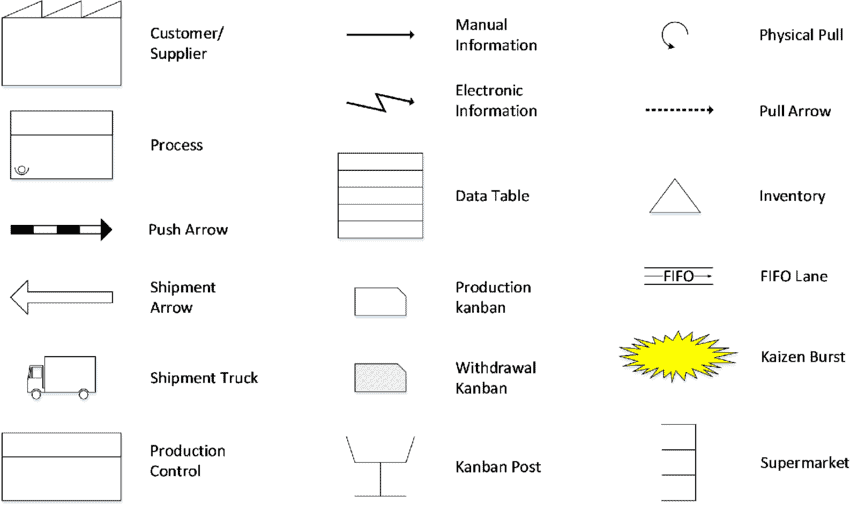
- Process Box: Represents a specific step in the process, often color-coded to indicate its significance.
- Material Flow: Illustrated as an arrow to show the movement of materials or products.
- Information Flow: Depicted as a dashed line with arrows, denoting the flow of information.
- Inventory: Shown as a triangle pointing to the inventory location.
- Manual Operation: Resembles a person, indicating tasks performed manually.
- Machine Operation: Depicted as a rectangle for tasks done by machines.
- Delay: Shown as a lightning bolt or clock to highlight waiting times.
- Transportation: An arrow inside a box symbolizes the movement of materials.
- Work Cell: Indicated by a U-shaped symbol, representing grouped operations.
- Supermarket: Represented as 'S' in a circle, signifying a storage point for materials.
- Kanban: Depicted as a square or rectangle with numbers, used for inventory control.
- Data Box: A rectangular shape with data and metrics related to the process.
- Push Arrow: An arrow pointing right for a push system.
- Pull Arrow: An arrow pointing left for a pull system.
- Customer/Supplier: Represents external entities like customers or suppliers.
Value Stream Mapping Examples
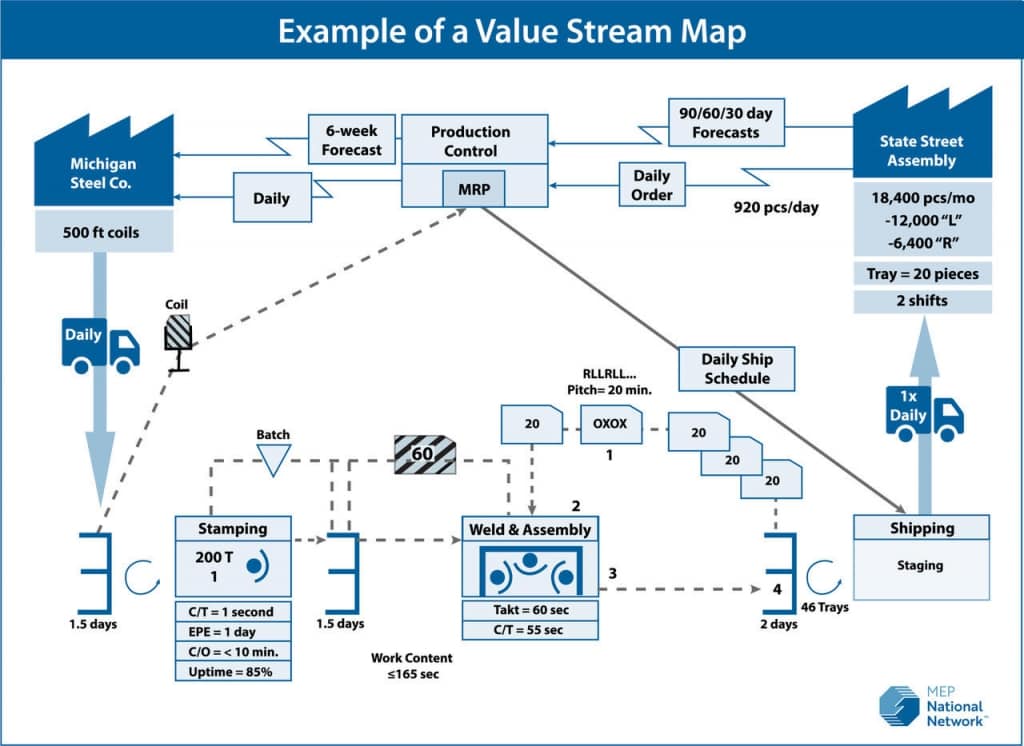
Here are some examples of value stream mapping:
- A manufacturing company uses VSM to map out the flow of materials and information for its production process. This helps the company to identify and eliminate waste, improve efficiency, and reduce costs.
- A healthcare organization uses VSM to map out the patient flow process. This helps the organization to identify and eliminate bottlenecks, improve efficiency, and reduce wait times.
- A software development company uses VSM to map out the software development process. This helps the company to identify and eliminate waste, improve efficiency, and reduce time to market for new products.
Final Thoughts
Value Stream Mapping is a valuable tool that empowers organizations to visualize, analyze, and enhance their processes. By identifying bottlenecks, eliminating waste, and optimizing workflows, businesses can streamline their operations, reduce costs, and ultimately improve customer satisfaction.
To maximize the benefits of Value Stream Mapping, it's crucial to facilitate effective team meetings and brainstorming sessions. AhaSlides can significantly enhance these gatherings. By using AhaSlides, teams can create engaging visual presentations, gather real-time feedback, and foster better communication among team members. It simplifies the process of sharing ideas, collaborating on improvements, and tracking progress, ultimately leading to more efficient and productive outcomes.
FAQs
What is meant by value stream mapping?
Value Stream Mapping (VSM) is a visual tool used to understand, analyze, and improve processes within an organization. It helps identify areas of waste, bottlenecks, and opportunities for optimization.
What are the 4 steps of value stream mapping?
4 Steps of Value Stream Mapping:
- Select: Choose the process to be mapped.
- Map: Create a visual representation of the current process.
- Analyze: Identify issues and areas for improvement.
- Plan: Develop a future state map with improvements.
What is co in value stream mapping?
"C/O" in Value Stream Mapping refers to "Changeover time," which is the amount of time required to set up a machine or process for producing a different product or part number.
Ref: Atlassian | Tallyfy | Lucid Chart