In the fast-paced business world, the key to staying ahead lies in continuous improvement. In this blog post, we embark on a journey to discover the 8 continuous improvement tools that help your organization towards constant enhancement. From time-tested classics to innovative solutions, we'll explore how these tools can make positive change, driving your team towards success.
Table Of Contents
- What Are The Continuous Improvement Tools?
- Continuous Improvement Tools
- Final Thoughts
- FAQs About Continuous Improvement Tools
Explore the Continuous Improvement toolkit
- Utilizing Hoshin Kanri Planning for Long-Term Success From Now
- Ishikawa Diagram Example | A Step-by-Step Guide for Effective Problem-Solving
- Five Whys Approach | Definition, Benefits, Application (+ Example)
- What Is Theory Of Constraints? A Simple Guide to Boosting Efficiency
- 6 Sigma DMAIC | A Roadmap to Operational Excellence
What Are The Continuous Improvement Tools?
Continuous improvement tools are tools, techniques, and methods used to improve efficiency, streamline processes, and promote ongoing development in organizations. This tool helps identify areas for improvement, supports problem-solving, and cultivates a culture of continuous learning and advancement within the organization.
Continuous Improvement Tools
Here are 10 continuous improvement tools and techniques that serve as guiding lights, illuminating the path to growth, innovation, and success.
#1 - PDCA Cycle: The Foundation of Continuous Improvement
At the heart of continuous improvement is the PDCA cycle – Plan, Do, Check, Act. This iterative process provides a structured framework for organizations to systematically drive improvement.
Plan:
Organizations start by identifying areas for improvement, setting goals, and planning. This planning phase involves analyzing existing processes, understanding the current state, and setting realistic goals.
Do:
The plan is then implemented on a small scale to test its effectiveness. This phase is important for gathering data and real-world insights. It involves implementing changes and closely monitoring the impact on target processes.
Check:
After implementation, the organization evaluates the results. This involves measuring performance against established goals, collecting relevant data, and evaluating whether changes are leading to the desired improvements.
Act:
Based on the assessment, make necessary adjustments. Successful changes are implemented on a larger scale, and the cycle begins again. The PDCA cycle is a dynamic tool that encourages continuous learning and adaptation.
#2 - Kaizen: Continuous Improvement from the Core
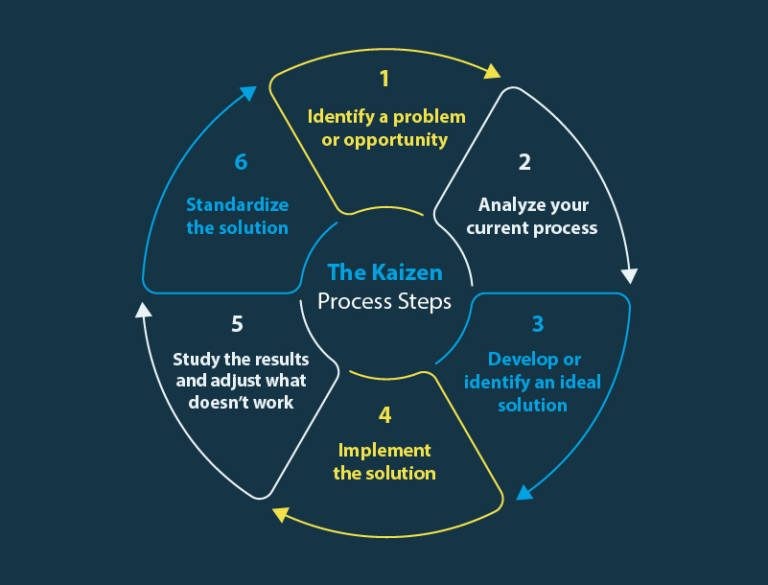
Kaizen, which means "change for the better," speaks to a philosophy of continuous improvement that emphasizes making small, incremental changes consistently to achieve significant improvements over time.
Small steps, big impact:
The continuous improvement process Kaizen involves all employees, from senior management to frontline employees. By promoting a culture of continuous improvement at every level, organizations empower their teams to identify and implement small changes that together lead to significant improvements.
Continuous learning:
Kaizen encourages a mindset of continuous learning and adaptation, builds on employee engagement, and harnesses the collective intelligence of the workforce to drive improvements in processes and systems.
#3 - Six Sigma: Driving Quality through Data
Continuous improvement tools Six Sigma is a data-driven methodology that aims to improve process quality by identifying and eliminating defects. It utilizes the DMAIC approach – Define, Measure, Analyze, Improve, and Control.
- Define: Organizations start by clearly defining the problem they want to solve. This involves understanding customer requirements and setting specific, measurable goals for improvement.
- Measure: The current state of the process is measured using relevant data and metrics. This phase involves collecting and analyzing data to identify the extent of the problem and its impact.
- Analyze: In this phase, the root causes of the problem are identified. Statistical tools and analysis techniques are employed to understand the factors contributing to defects or inefficiencies.
- Improve: Based on the analysis, improvements are made. This phase focuses on optimizing processes to eliminate defects and improve overall efficiency.
- Control: To ensure sustained improvement, control measures are put in place. This includes continuous monitoring and measurement to maintain the benefits achieved through improvements.
#4 - 5S Methodology: Organizing for Efficiency
The 5S methodology is a workplace organization technique aimed at improving efficiency and safety. The five S's – Sort, Set in order, Shine, Standardize, Sustain – provide a structured approach to organizing and maintaining a productive work environment.
- Sort: Eliminate unnecessary items, reducing waste and boosting efficiency.
- Set in Order: Organize remaining items systematically to minimize search time and optimize workflow.
- Shine: Prioritize cleanliness for improved safety, enhanced morale, and increased productivity.
- Standardize: Establish and implement standardized procedures for consistent processes.
- Sustain: Cultivate a culture of continuous improvement to ensure lasting benefits from 5S practices.
#5 - Kanban: Visualizing Workflow for Efficiency

Kanban is a visual management tool that helps teams manage work by visualizing workflow. Originating from lean manufacturing principles, Kanban has found widespread application in various industries to improve efficiency and reduce bottlenecks.
Visualizing Work:
Kanban uses visual boards, typically divided into columns representing different stages of a process. Each task or work item is represented by a card, allowing teams to easily track progress and identify potential issues.
Limiting Work in Progress (WIP):
To work efficiently, Kanban recommends limiting the number of tasks in progress simultaneously. This helps prevent overburdening the team and ensures that work is completed efficiently before new tasks are started.
Continuous Improvement:
The visual nature of Kanban boards facilitates continuous improvement. Teams can quickly identify areas of delay or inefficiency, allowing for timely adjustments to optimize workflow.
#6 - Total Quality Management (TQM)
Total Quality Management (TQM) is a management approach that focuses on long-term success through customer satisfaction. It involves continuous improvement efforts in all aspects of the organization, from processes to people.
Customer-Centric Focus:
Understanding and meeting the needs of customers is a primary focus of Total Quality Management (TQM). By consistently delivering quality products or services, organizations can build customer loyalty and enhance their competitive advantage.
Continuous Improvement Culture:
TQM requires a cultural shift within the organization. Employees at all levels are encouraged to participate in improvement initiatives, fostering a sense of ownership and accountability for quality.
Data-Driven Decision-Making:
TQM relies on data to inform decision-making. Continuous monitoring and measurement of processes allow organizations to identify areas for improvement and make informed adjustments.
#7 - Root Cause Analysis: Digging Deeper for Solutions
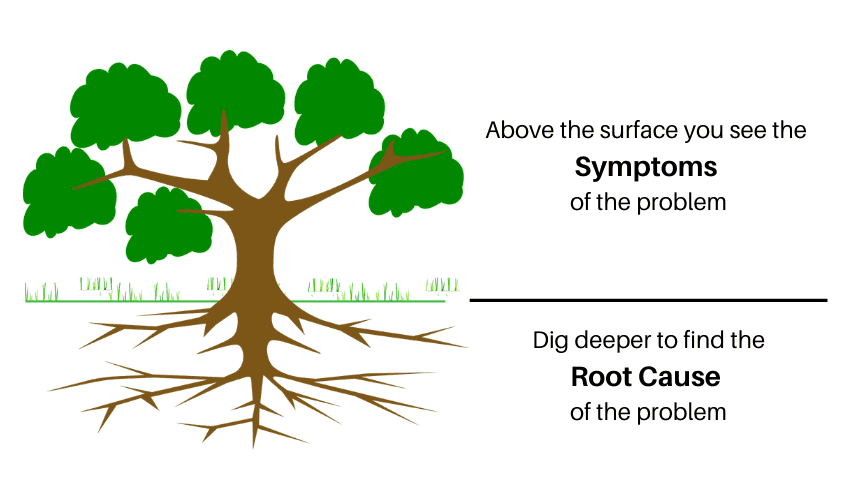
Root cause analysis method is a methodical process for identifying the underlying cause of a problem. By addressing the root cause, organizations can prevent the recurrence of issues.
Fishbone Diagrams (Ishikawa):
This visual tool helps teams systematically explore potential causes of a problem, categorizing them into various factors such as people, processes, equipment, and environment.
5 Whys:
The 5 Whys technique involves asking "why" repeatedly to trace the root cause of a problem. By digging deeper with each "why," teams can uncover the fundamental issues contributing to a problem.
Fault Tree Analysis:
This method involves creating a graphical representation of all possible causes of a specific problem. It helps identify contributing factors and their relationships, aiding in the identification of the root cause.
#8 - Pareto Analysis: The 80/20 Rule in Action
Pareto Analysis, based on the 80/20 rule, helps organizations prioritize improvement efforts by focusing on the most significant factors contributing to a problem.
- Identifying the Vital Few: This analysis involves identifying the vital few factors that contribute to the majority (80%) of the problems or inefficiencies.
- Optimizing Resources: By concentrating efforts on addressing the most impactful issues, organizations can optimize resources and achieve more significant improvements.
- Continuous Monitoring: Pareto Analysis is not a one-time activity; it requires continuous monitoring to adapt to changing circumstances and ensure sustained improvement.
Final Thoughts
Continuous improvement is about refining processes, fostering innovation, and nurturing a growth culture. The success of this journey hinges on strategically combining diverse Continuous improvement tools, from the structured PDCA cycle to the transformative Kaizen approach.
Looking ahead, technology is a key driver for improvement. AhaSlides, with its templates and features, enhances meetings and brainstorming, providing a user-friendly platform for effective collaboration and creative sessions. Using tools like AhaSlides helps organizations stay nimble and bring innovative ideas into every aspect of their ongoing improvement journey. By streamlining communication and collaboration, AhaSlides enables teams to work more efficiently and effectively.
FAQs About Continuous Improvement Tools
What are the 3 methods to continuous improvement?
PDCA Cycle (Plan-Do-Check-Act), Kaizen (Continuous small improvements), and Six Sigma (Data-driven methodology).
What are CI tools and techniques?
Continuous Improvement Tools and techniques are PDCA Cycle, Kaizen, Six Sigma, 5S Methodology, Kanban, Total Quality Management, Root Cause Analysis, and Pareto Analysis.
Is kaizen a continuous improvement tool?
Yes, Kaizen is a continuous improvement tool that originated in Japan. It is based on the philosophy that small, incremental changes can lead to significant improvements over time.
What are examples of continuous improvement program?
Examples of Continuous Improvement Programs: Toyota Production System, Lean Manufacturing, Agile Management and Total Productive Maintenance (TPM).
What is Six Sigma tools?
Six Sigma Tools: DMAIC (Define, Measure, Analyze, Improve, Control), Statistical Process Control (SPC), Control Charts, Pareto Analysis, Fishbone Diagrams (Ishikawa) and 5 Whys.
What is the 4 a continuous improvement model?
The 4A Continuous Improvement Model consists of Awareness, Analysis, Action, and Adjustment. It guides organizations through recognizing the need for improvement, analyzing processes, implementing changes, and continuously adjusting for sustained progress.