In the dynamic business world, the key to staying ahead lies in focusing on making improvements systematically. Enter the PDCA cycle – a game-changer for organizations striving for excellence.
In this blog post, we’ll walk you through the simplicity and impact of Plan-Do-Check-Act, examples of the PDCA cycle in various industries, and provide tips for organizations looking to boost team brilliance and navigate the path to success.
Table Of Contents
- What Is PDCA Cycle?
- The Four Stages Of The PDCA Cycle
- PDCA Cycle Benefits
- Examples Of PDCA Cycle
- 5 Practical Tips for Maximum Impact Of PDCA Cycle
- Key Takeaways
- FAQs
What Is PDCA Cycle?
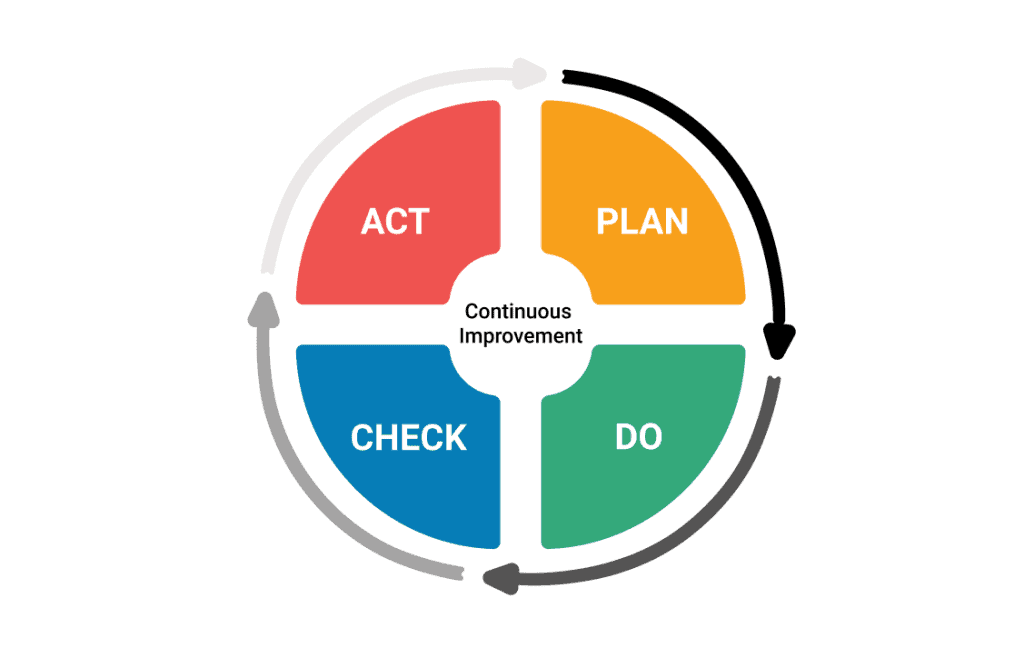
The PDCA cycle, also known as the Deming Cycle or Plan-Do-Check-Act cycle, is a straightforward and powerful method for continuous improvement. It’s a systematic approach designed to enhance processes and achieve better results over time.
Comprising four iterative phases – Plan, Do, Check, and Act – this cycle provides a systematic framework that organizations use to enhance processes, products, or services. Each phase plays a crucial role in fostering a culture of continuous improvement and adaptability
The Four Stages Of The PDCA Cycle
Let’s break down the four stages of the PDCA cycle:
1/ Plan: Defining the Path Forward
The first phase of the cycle is Plan, and its primary objective is to set a clear course for improvement. In this stage, organizations identify a problem or an opportunity for enhancement and establish measurable objectives. The emphasis is on careful planning, ensuring that the objectives align with the overall goals of the organization.
During the planning phase, teams need to:
- Analyze the current situation and identify the underlying reasons for it.
- Develop a detailed plan to address identified issues, including specific actions, required resources, and a timeline for implementation.
- The key principle underlying the Plan phase is the creation of constancy of purpose toward improvement.
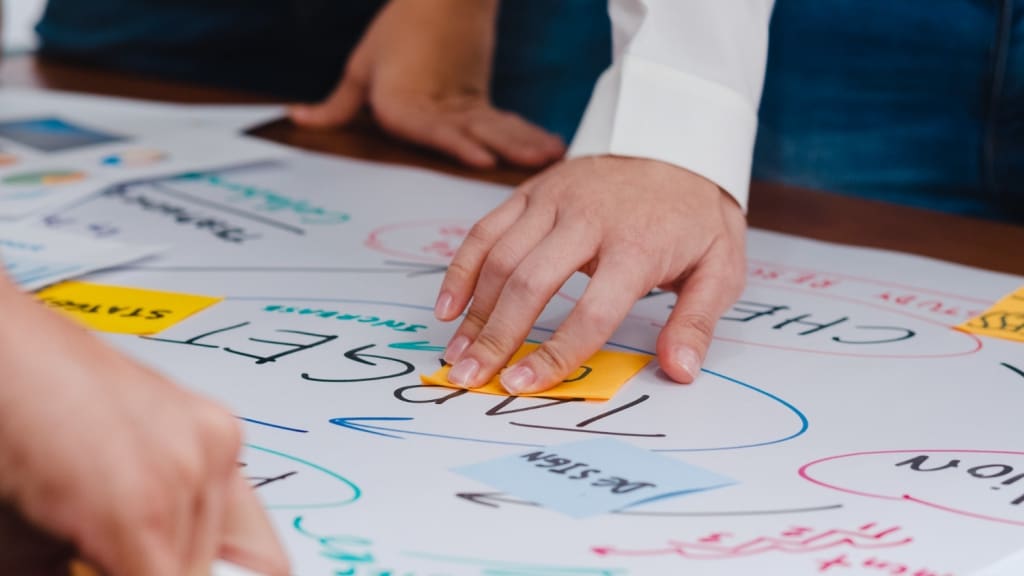
2/ Do: Implementing the Plan in Action
With a well-thought-out plan in hand, the organization moves to the Do phase, where the proposed changes are put into action. This stage is often considered a trial or a test phase, and the changes are typically implemented on a small scale or in a controlled environment. The objective is to observe how the plan performs in real-world conditions.
In the Do phase, organizations are encouraged to
- Embrace a proactive and innovative mindset,
- Test and experiment with new ideas.
- Closely monitor the implementation
- Document any challenges or unexpected issues for further analysis.
3/ Check: Assessing the Results
After the changes have been implemented, the Check phase comes into play.
- This stage involves evaluating the results and comparing them against the objectives set in the planning phase.
- Data collection and analysis are essential components of the Check phase, providing insights into the effectiveness of the implemented changes.
4/ Act: Adjusting and Standardizing for Ongoing Improvement
Based on the evaluation in the Check phase, the organization proceeds to the Act phase.
This stage involves making decisions and taking actions based on the lessons learned during the evaluation.
- If the changes are successful, the organization works to standardize them, incorporating them into regular operations.
- If issues are identified during the Check phase, the plan will be adjusted and the PDCA cycle will restart.
The Act phase is a continuous loop, representing the commitment to adapt and refine processes continually.
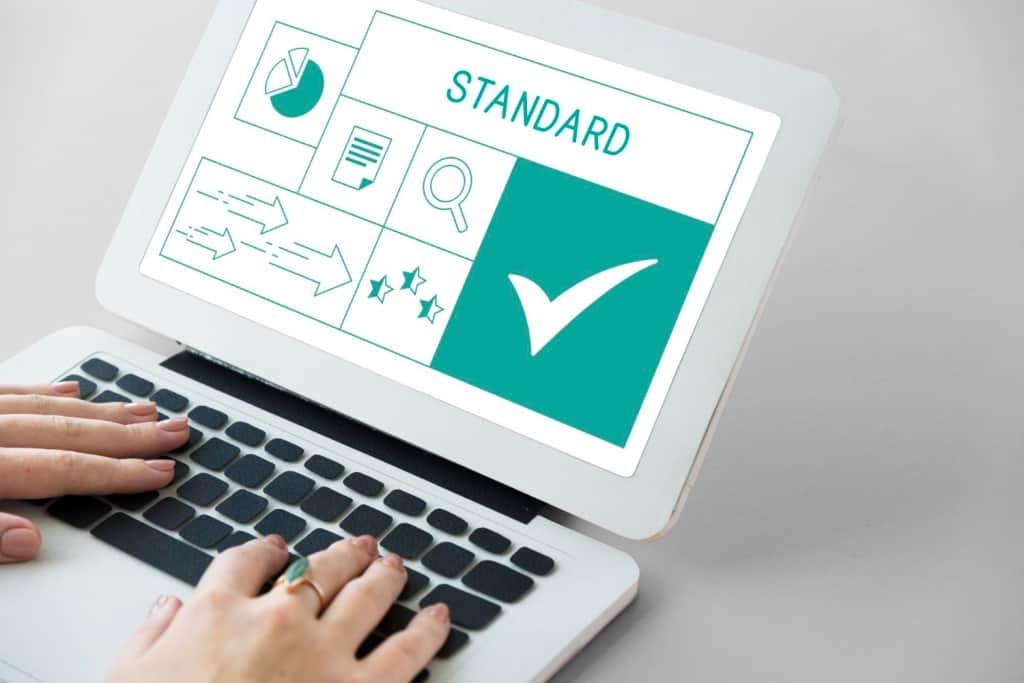
PDCA Cycle Benefits
This cycle offers several benefits, emphasizing continuous improvement and efficiency. Here are four main benefits:
Continuous Improvement:
PDCA is all about getting better. By regularly cycling through the phases, organizations can continually refine processes, identify areas for improvement, and make incremental advancements.
Data-Driven Decision Making:
To ensure that decisions are based on evidence and actual outcomes, it is important to gather and analyze data during each phase of the PDCA cycle.
This data-driven approach leads to more informed decision-making and increases the likelihood of successful changes. By using evidence instead of assumptions, organizations can make better choices.
Risk Reduction and Controlled Implementation:
The PDCA cycle allows to test changes on a small scale during the “Do” phase. This controlled implementation minimizes the risk of large-scale failures.
By identifying and addressing issues early on, organizations can improve their strategies before full implementation, reducing potential negative impacts.
Engagement and Empowerment:
PDCA encourages collaboration and involvement from all levels of an organization.
Team members work together in planning, executing, reviewing, and adjusting phases. This collaborative effort creates a sense of ownership and engagement, leading to a shared commitment to progress and a supportive team environment.
Examples Of PDCA Cycle
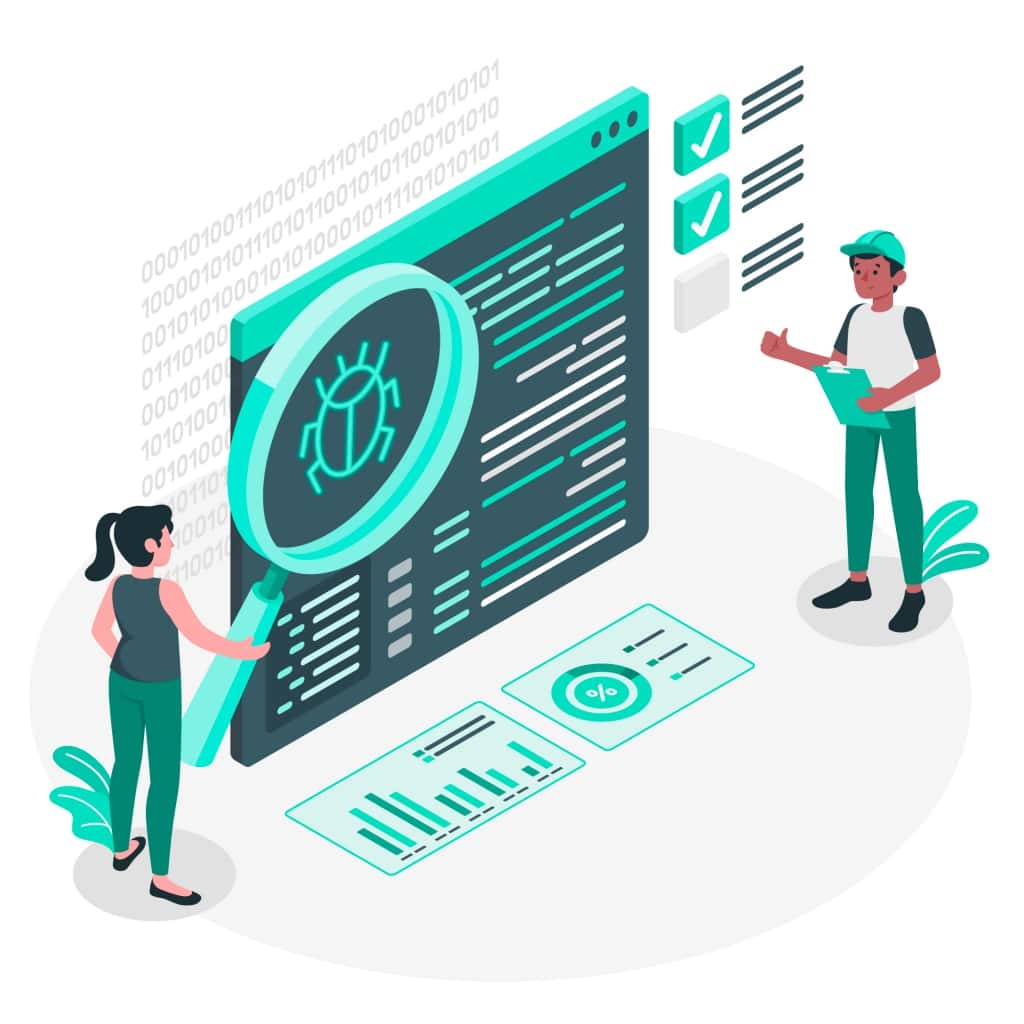
Here are some examples of the PDCA Cycle:
PDCA Cycle in Quality Management:
In quality management, this cycle is a fundamental tool for ensuring continuous improvement. Here’s a brief overview:
- Plan: Define quality objectives and identify processes that need improvement.
- Do: Implement changes in a controlled manner, often starting with a pilot project.
- Check: Evaluate results against predetermined objectives, using data and feedback.
- Act: Standardize successful changes and integrate them into the overall quality management system.
PDCA Cycle Example in Healthcare:
In healthcare, this cycle can enhance patient care and operational efficiency:
- Plan: Identify areas for improvement, such as reducing patient wait times.
- Do: Implement changes, such as optimizing appointment scheduling.
- Check: Assess the impact on wait times and patient satisfaction.
- Act: Adjust scheduling procedures accordingly and apply improvements across the healthcare facility.
PDCA Cycle in Nursing:
For nursing processes, this cycle aids in refining patient care and workflows:
- Plan: Set goals like improving patient communication during shift changes.
- Do: Implement changes, such as adopting a standardized communication protocol.
- Check: Evaluate communication effectiveness and nurse satisfaction.
- Act: Standardize the effective communication methods and integrate them into nursing procedures.
PDCA Cycle Example in Manufacturing:
In manufacturing, this cycle ensures product quality and process efficiency:
- Plan: Define quality standards and identify areas for production improvement.
- Do: Implement changes, like adjusting machine settings or refining assembly processes.
- Check: Inspect products and analyze production data for improvements.
- Act: Standardize successful changes and incorporate them into standard operating procedures.
PDCA Cycle Example in the Food Industry:
In the food industry, the cycle supports quality control and safety measures:
- Plan: Set food safety goals, such as reducing the risk of contamination.
- Do: Implement changes, like modifying sanitation procedures.
- Check: Monitor food safety metrics and inspect for compliance.
- Act: Standardize effective sanitation practices and integrate them into food safety protocols.
Example of PDCA Cycle in Personal Life:
Even in personal life, the cycle can be applied for continuous self-improvement:
- Plan: Set personal goals, like improving time management skills.
- Do: Implement changes, such as adopting a new scheduling method.
- Check: Assess the impact on daily productivity and personal satisfaction.
- Act: Adjust the schedule as needed and standardize effective time management practices.
This cycle is a versatile and universally applicable methodology, adaptable to various industries and personal contexts, promoting a systematic approach to continuous improvement.
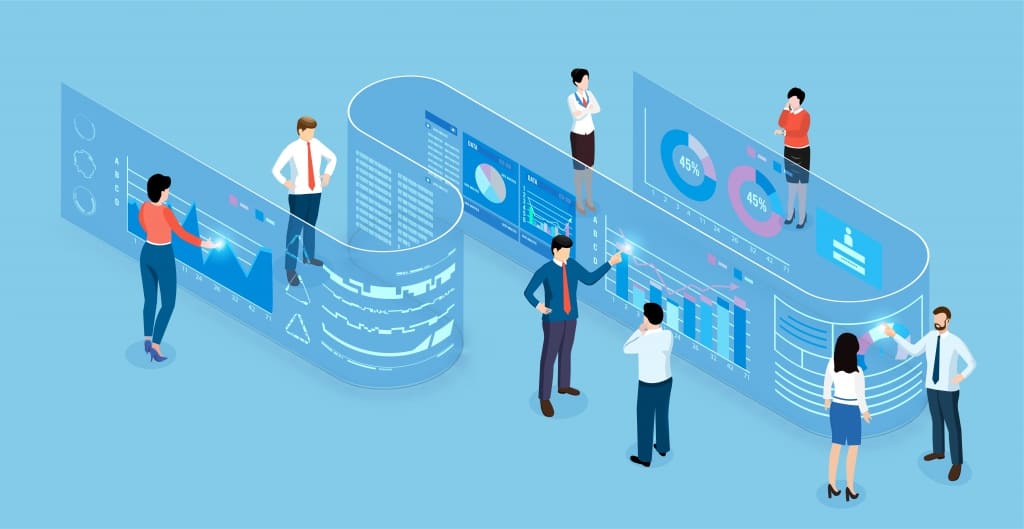
5 Practical Tips for Maximum Impact Of PDCA Cycle
- Clearly Define Objectives: Begin with well-defined and measurable objectives. Clearly articulate what you aim to achieve during each cycle.
- Engage Stakeholders: Involve relevant stakeholders in the planning phase. Their input is valuable for identifying problems, setting objectives, and proposing solutions.
- Thoroughly Analyze the Current State: Before planning, conduct a comprehensive analysis of the current situation. This helps in identifying root causes and understanding the context of the improvement effort.
- Start Small with Do Phase: During the Do phase, implement changes on a small scale or in a controlled environment. This minimizes risks and allows for a more manageable assessment.
- Collect Relevant Data: Ensure you collect sufficient data during the Check phase. This data provides the basis for evaluating the effectiveness of the changes and making informed decisions.
- Use Visual Tools: Utilize visual aids, such as flowcharts or diagrams, to map out the PDCA cycle. This enhances understanding and communication among team members.
Key Takeaways
The PDCA cycle stands as a compass for organizations and individuals navigating the journey of continuous improvement. Its four phases – Plan, Do, Check, and Act – provide a simple yet powerful framework for problem-solving and achieving excellence.
In today’s fast-paced world, effective communication and collaboration are key components of successful implementation. A tool like AhaSlides can enhance meetings and brainstorming sessions. Through its user-friendly interface and interactive features, AhaSlides facilitates the exchange of ideas, data analysis, and real-time feedback, making the PDCA cycle even more accessible and impactful.
FAQs
What is the PDCA Cycle Process?
The PDCA (Plan-Do-Check-Act) cycle is a systematic process for continuous improvement. It involves planning, implementing changes, checking results, and acting based on those results to refine and enhance processes.
What is the PDSA Cycle?
The PDSA cycle, also known as the Plan-Do-Study-Act cycle, and the PDCA cycle are essentially the same. In healthcare settings, PDSA and PDCA are often used interchangeably. Both cycles follow a four-step approach to continuous improvement.
What is the PDCA Cycle Summary?
The PDCA cycle is a simple and effective method for problem-solving and continuous improvement. It consists of four phases: Plan (identify and plan for improvement), Do (implement the plan on a small scale), Check (evaluate the results), and Act (standardize successful changes and repeat the cycle).
Ref: ASQ | Mind Tools