Operational Excellence (OpEx) is a crucial strategy that helps organizations optimize business operations and improve performance. It focuses on continuous improvement, enhancing productivity and quality, saving costs, and achieving sustainable competition in the market.
In this article, we will explore some real-world operational excellence examples as well as define what operational excellence is. By examining these examples, we can gain insights into how these companies have applied these principles to achieve exceptional results and how we can apply these strategies to our businesses.
Who created the term 'Operational Excellence'? | Dr. Joseph M. Juran |
When was the term 'Operational Excellence' invented? | 1970s |
Three main criteria of 'Operational Excellence'? | Customer satisfaction, empowerment and ongoing improvement |
Table of Contents
- #1 - What Is Operational Excellence?
- #2 - Why Is Operational Excellence Important?
- #3 - Who Benefits From Operational Excellence?
- #4 - When Should Operational Excellence Be Implemented?
- #5 - Where Can Operational Excellence Be Applied?
- #6 - Common Tools And Methods Of Operational Excellence
- #7 - How To Implement Operational Excellence
- #8 - Best Operational Excellence Examples
- Key Takeaways
- Frequently Asked Questions
#1 - What Is Operational Excellence?
Operational Excellence is a strategy for optimizing business operations to improve efficiency, reduce waste, and enhance the quality of products or services delivered to customers.
It involves a range of methods, tools, and processes to optimize the efficiency and performance of the organization.
Operational Excellence aims to:
- Create a culture of continuous improvement where all employees are engaged in the process of optimizing operations.
- Maximize value for customers and achieve sustainable competition in the market.
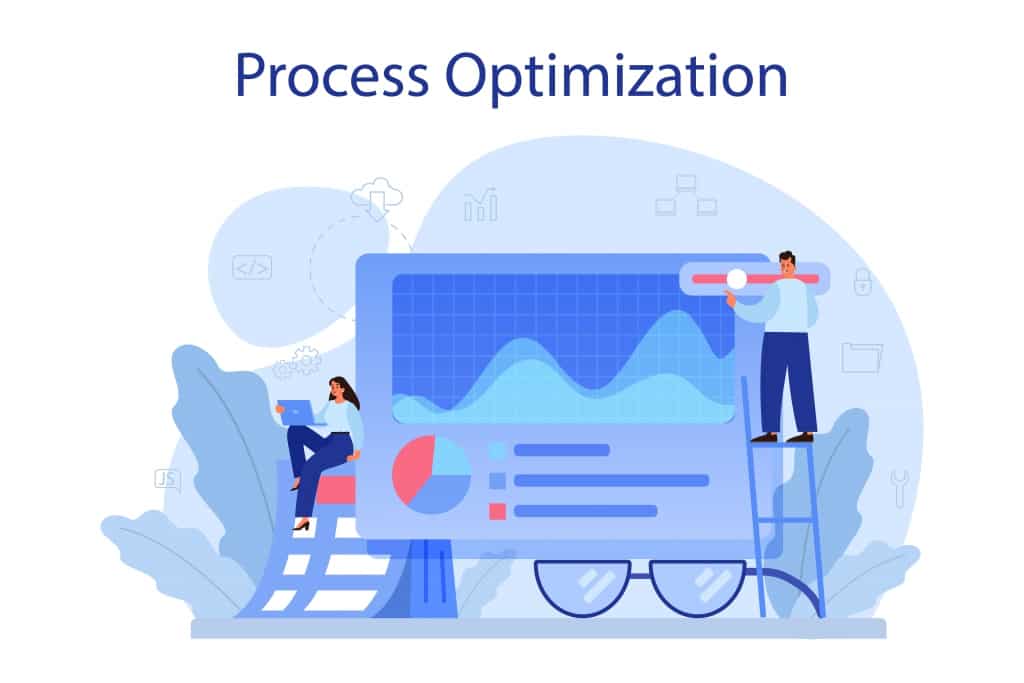
Operational Excellence tools and methods include Lean, Six Sigma, Kaizen, Total Quality Management (TQM), Business Process Reengineering (BPR), Customer Relationship Management (CRM), and many more. These tools help organizations optimize processes, boost productivity and quality, save costs, and enhance the customer experience.
- For example, A food manufacturing company can apply Operational Excellence to improve customer service. This can involve implementing a customer relationship management (CRM) system to track customer interactions and identify areas for improvement. By providing more professional and personalized customer service, the company can improve customer satisfaction and loyalty, leading to increased sales and revenue.
#2 - Why Is Operational Excellence Important?
Here are the key reasons why Operational Excellence matters:
- Increase efficiency: Operational Excellence can help optimize production processes and other business activities, thereby reducing production costs and improving profits.
- Improve product and service quality: Operational Excellence helps organizations optimize production processes and minimize errors to improve product and service quality. It leads to better products/services, increases customer satisfaction, and strengthens their brand reputation.
- Create sustainable competition: Organizations that adopt Operational Excellence can produce high-quality products and services at a lower cost. So they can attract new customers while retaining existing customers well.
- Encourage sustainability: When optimizing production processes and sustainably using resources, organizations can reduce the impact of business activities on the environment and help organizations grow sustainably into the future.
#3 - Who Benefits From Operational Excellence?
The Operational Excellence strategy creates a win-win situation for all, including employers, employees, customers, and shareholders.
- For Employers: This strategy can help employers improve their bottom line and create a successful and sustainable business.
- For Employees: Using Operational Excellence can create a safer, more efficient workplace, improved training and development opportunities, and better job security.
- For Customers: Operational Excellence can result in higher quality products and services, faster delivery times, and more responsive customer service.
- For Shareholders: Operational Excellence can lead to increased profitability, improved financial performance, and higher shareholder value.
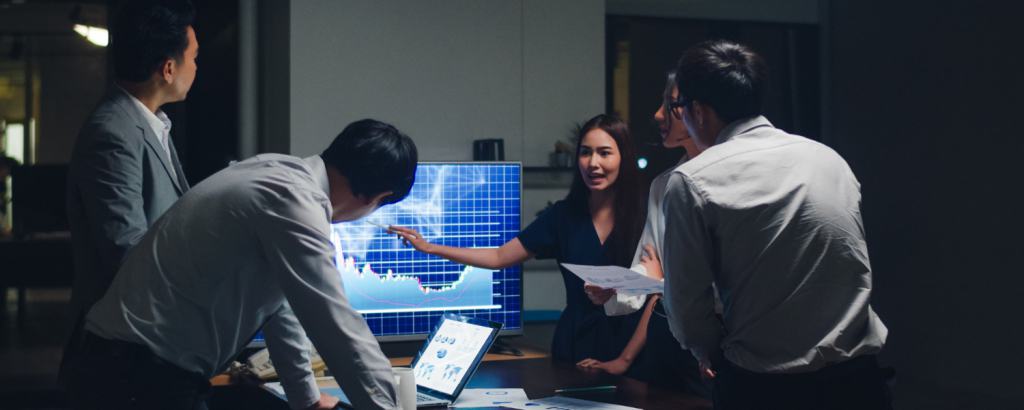
#4 - When Should Operational Excellence Be Implemented?
Organizations can adopt Operational Excellence at any time, but there are certain situations when it can be especially beneficial as follows:
- When business and production processes are inefficient and experiencing problems.
- When production and business costs are high or increasing.
- When the quality of products and services does not meet the customers' requirements.
- When organizational structures and production processes are not optimized.
- When competitive opportunities are at stake, the organization needs to improve its performance to compete in the market.
- When the organization is looking to promote sustainable development and ensure the future of the business.
Here are some specific examples of when an organization may want to consider implementing Operational Excellence:
- A healthcare provider is trying to handle extensive appointment scheduling processes and patient wait times. The provider decides to implement Operational Excellence to optimize their workflow and improve the patient experience, which results in shorter wait times and better patient satisfaction.
- A start-up company is growing rapidly and wants to scale its operations to meet demand. The company applies Operational Excellence to ensure its processes are efficient and sustainable, allowing it to continue expanding without sacrificing quality or incurring high costs.
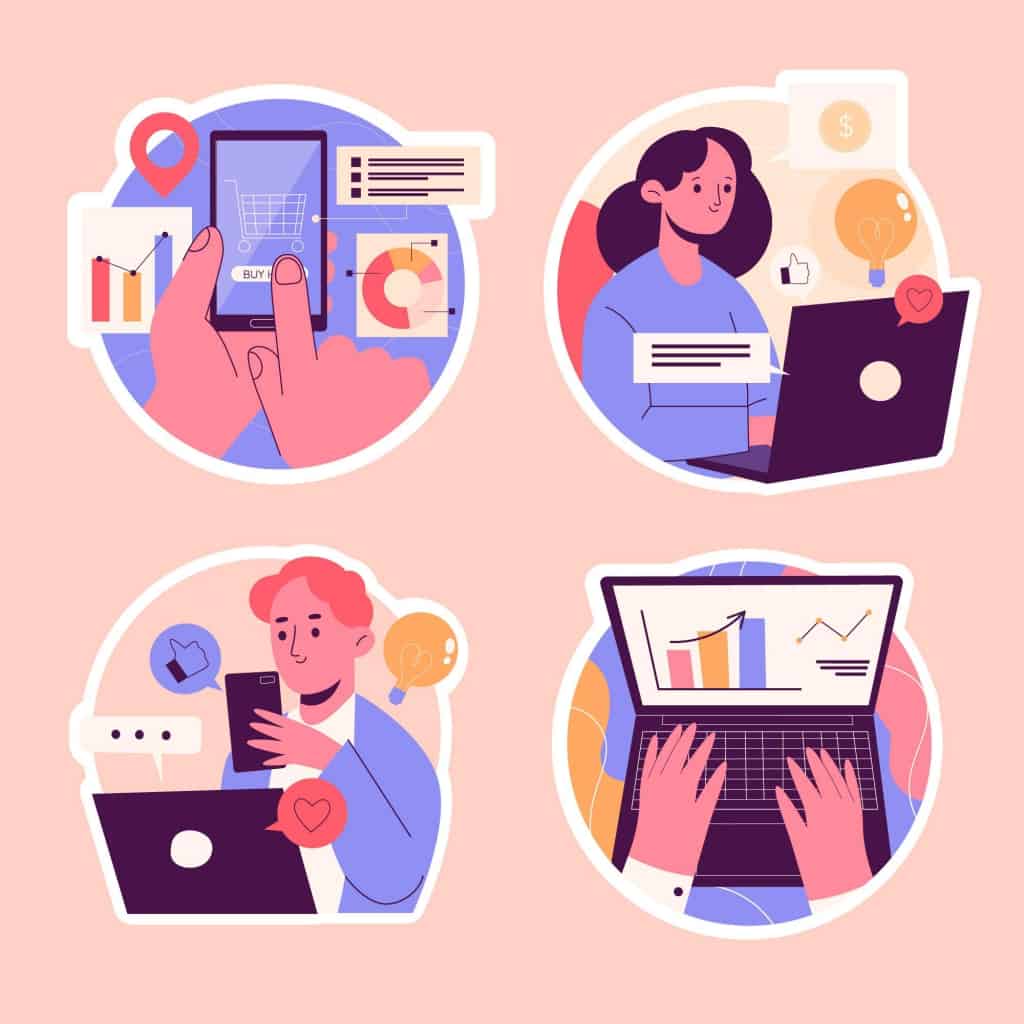
#5 - Where Can Operational Excellence Be Applied?
Any organization that wants to optimize its production processes or business operations can apply Operational Excellence.
Manufacturing, services, supply chain management, healthcare, education, government, and many more industries can all use the Operational Excellence strategy. It can also be used at any scale, from small firms to global corporations.
#6 - Common Tools And Methods Of Operational Excellence
Operational Excellence uses a variety of tools and methods to achieve the goal of optimizing production and business processes. Here are 4 commonly used tools and methods in Operational Excellence:
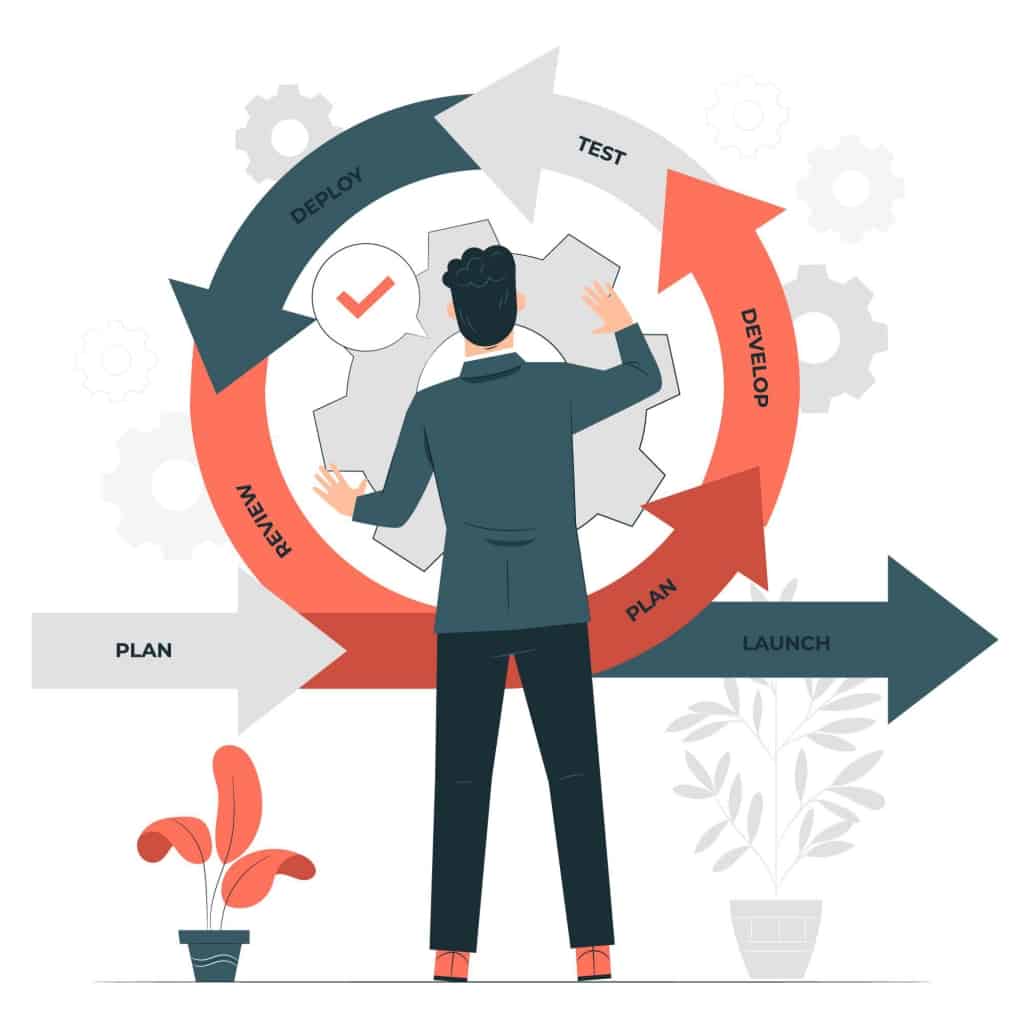
1/ Lean Manufacturing
Lean Manufacturing is one of the important tools of Operational Excellence. This approach focuses on optimizing production processes by minimizing wasteful activities and optimizing resource usage.
There are 5 basic principles of Lean Manufacturing:
- Value: Define value from the customer's point of view and focus on delivering that value by optimizing the manufacturing process.
- Value Stream: Define the value stream (the process from which a product is manufactured to when it is delivered to the customer) and optimize this stream.
- Flow Creation: Create a consistent production flow to ensure that products are produced at the right time and in sufficient quantities to meet customer needs.
- No Waste: Reduce all types of waste in the production process, including time, resources, and materials.
- Continuous Improvement: Continually improve manufacturing processes to increase productivity, reduce costs, and increase product quality.
2/ Six Sigma
The Six Sigma methodology focuses on minimizing errors in production and business processes through statistical tools and techniques. The DMAIC steps to implement Six Sigma include
- Definition: Identify the problem to be solved and set a specific goal.
- Measure: Measure the process by collecting data related to production and business processes.
- Analysis: Use statistical tools and techniques to analyze data and determine the cause of problems.
- Improvement: Develop and implement solutions to fix problems and improve processes.
- Control: Ensure that implemented solutions achieve their goals, and monitor production and business processes to detect and fix arising issues.
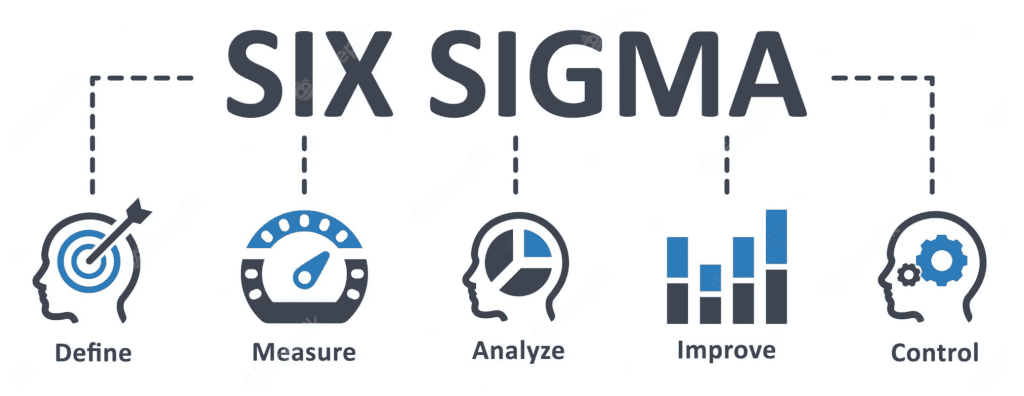
3/ Kaizen
Kaizen is a method of continuous process improvement that focuses on finding and eliminating bugs, problems, and minor issues in production and business processes.
With the Kaizen method, employees are encouraged to provide input to improve processes and create a positive work environment to achieve continuous and sustainable change.
Here are specific steps of the Kaizen method:
- Identify improvement goals and problems to be solved.
- Organize work groups to solve problems, and find solutions.
- Collect and analyze data to assess the current state of the process.
- Suggest improvements and make small changes to improve the process.
- Test and evaluate improvements to ensure effectiveness and continue to improve the process.
4/ Total Quality Management
Total Quality Management (TQM) is a comprehensive quality management method that focuses on improving product and service quality throughout the whole manufacturing and business process.
TQM encompasses activities and tools for quality assurance: from setting quality operational excellence objectives to evaluating product quality, and from developing processes to training staff programs.
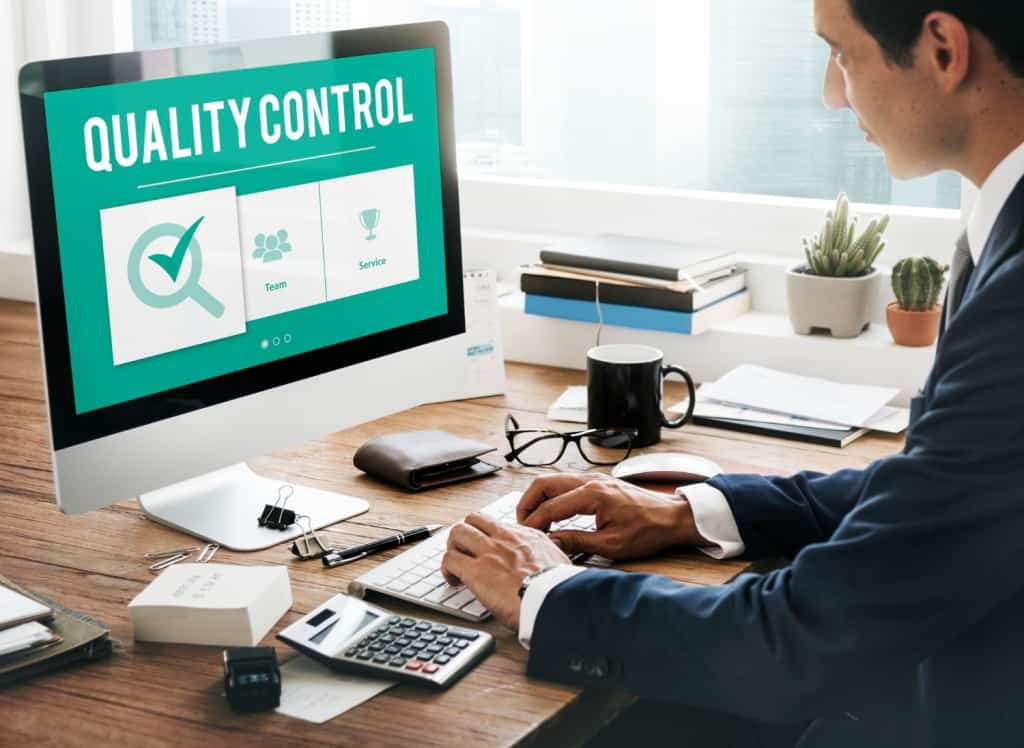
#7 - How To Implement Operational Excellence
The process of implementing Operational Excellence can vary by organization and industry. Here are some general steps in the implementation of Operational Excellence:
1/ Define strategic goals and plans
First, organizations need to define their goals to ensure that Operational Excellence is working towards them. They then can develop a strategic plan to implement Operational Excellence.
2/ Assess the status quo and identify problems
Then, they have to assess the current state of their manufacturing processes and other business activities to identify problems or waste.
3/ Apply Operational Excellence Tools and Methods
After problems are found, organizations can apply Operational Excellence tools and methods to optimize production processes and other business activities. These tools and methods can include Lean Six Sigma, Kaizen, TPM, and more.
4/ Employee Training
An important part of implementing Operational Excellence is training employees so they can understand and implement new processes. Organizations need to ensure that their employees are professional to optimize their production processes.
5/ Monitoring and Evaluation
Finally, organizations have to monitor and evaluate production processes and other business activities to ensure that new processes are being implemented effectively.
They can come up with performance indicators and track them to ensure that new processes are working properly.
#8 - Best Operational Excellence Examples
Here are 6 concrete examples of how Operational Excellence is implemented across corporations around the world:
1/ Toyota Production System - Operational Excellence Examples
Toyota was one of the first companies to implement Lean Manufacturing and apply it to their production process. They have focused on eliminating waste and optimizing processes to improve product quality and increase productivity.
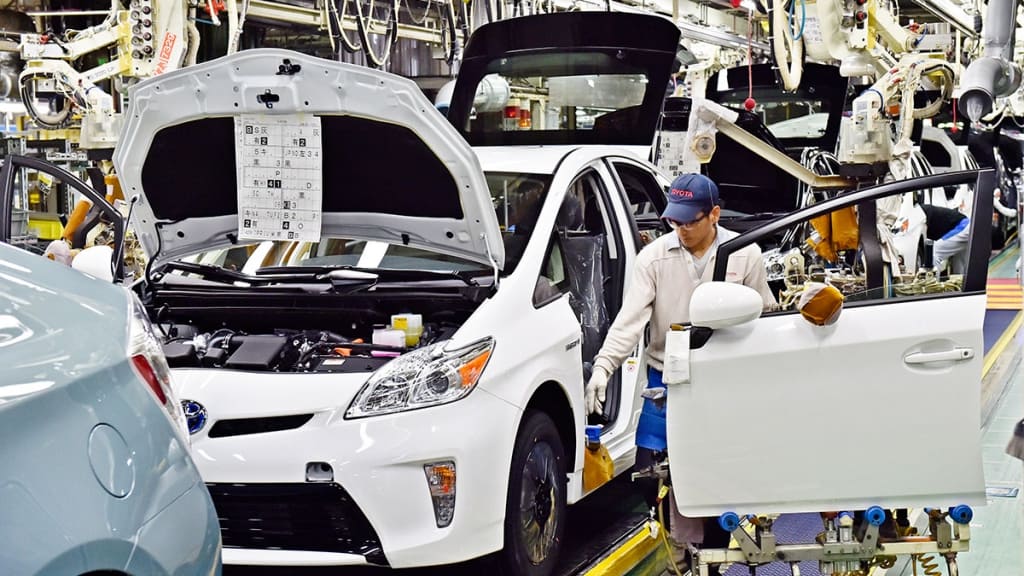
2/ Starbucks - Operational Excellence Examples
Starbucks has focused on improving its manufacturing and serving processes to ensure the best product quality and customer experience possible.
They have had an extensive training program to train staff in quality and customer service, and have used technology to optimize processes and increase their flexibility in serving customers.
3/ Marriott International - Operational Excellence Examples
Marriott International is an example of Total Quality Management (TQM).
They improve the quality of products and services by setting strict standards and creating a positive work environment to ensure everyone in the organization is committed to quality.
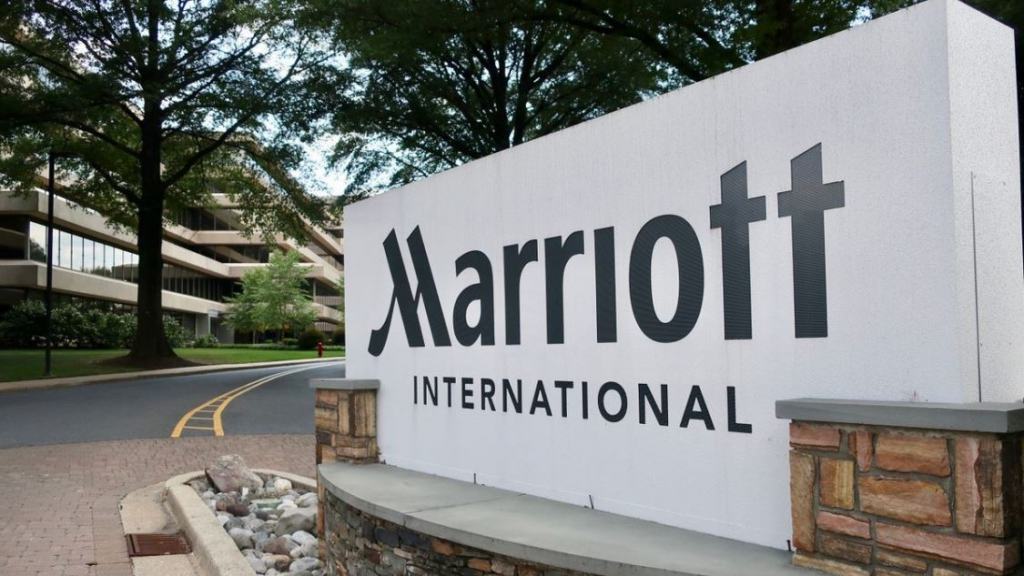
4/ General Electric (GE) - Operational Excellence Examples
GE is an example of applying Six Sigma in Operational Excellence - Operational Excellence Examples.
GE has implemented Six Sigma across the entire organization and has achieved great success in terms of process optimization and product quality improvement.
5/ Southwest Airlines - Operational Excellence Examples
Southwest Airlines has created a unique business model based on waste reduction and process optimization to provide high-quality service at reasonable prices.
They use information technology to manage bookings, optimize schedules and enhance staff training to ensure service quality.
6/ Amazon - Operational Excellence Examples
Amazon is an example of Agile, an agile project management approach that focuses on quick interaction and feedback from customers and employees.
Amazon uses Agile to develop new products, improve processes, and increase organizational agility.
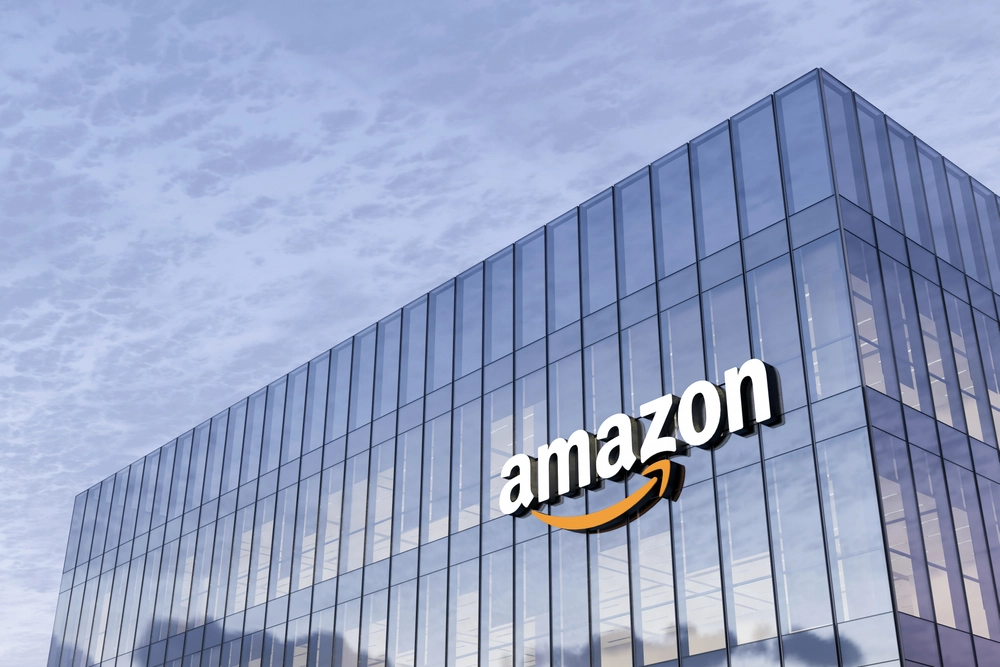
Key Takeaways
Hopefully, the top 6 Operational Excellence Examples above can give you an overview of this strategy. Operational Excellence is important for any organization looking to improve quality, optimize processes and increase operational efficiency. Its methods and tools are all aimed at improving product/service quality, minimizing waste, optimizing resources, and increasing competitiveness.
Frequently Asked Questions
What is Operational Excellence?
Operational Excellence is a management strategy that focuses on improving processes, reducing waste, increasing efficiency, and continuously improving quality to achieve business goals.
What are the benefits of Operational Excellence?
The benefits of Operational Excellence include improved productivity, increased profitability, better customer satisfaction, enhanced employee engagement, and a more efficient and effective organization overall.
How long does it take to see results from Operational Excellence?
The time it takes to see results from Operational Excellence varies depending on the scope and complexity of the implementation. Some organizations may see results within a few weeks or months, while others may take several years to fully implement and see significant results.